مخازن تحت فشار
مخازن تحت فشار چیست؟
مخازن تحت فشار (Pressure Vessel) نوعی تجهیزات صنعتی است که برای ذخیره بخار، گازها و مایعات به کار میرود. در مخزن تحت فشار میتوان بیش از 15 پوند بر هر اینچ مربع این مواد را ذخیره کرد. مخزن تحت فشار در استخراج معدن، پالایشگاه ها، و تجهیزات نظامی مانند زیر دریایی ها استفاده میشود. از این مخازن برای ذخیره گازهایی مانند کلرین، آمونیاک و مایعاتی مانند نفت استفاده میشود.
مخازن تحت فشار برای کاربردهای صنعتی به کار میروند. این مخازن همیشه در معرض خطر قرار دارند. این مخازن با مجوزهای مهندسی ساخته میشود. بازرسی های این نوع مخازن لازم است که در چندین مرحله و با دقت به انجام برسد. هر چقدر که بازرسی ها سخت گیرانه باشد به همان اندازه ایمنی این مخازن نیز بیشتر خواهد بود.
انواع مخازن تحت فشار
مخازن تحت فشار برای حفظ و نگهداری مایعات استفاده میشود. از اتوکلاوهایی برای مواد تولید میشود. هدف از ساخت اتوکلاو، افزایش فشار به دما به حد معینی که بتوان آن را کنترل کرد. ضد عفونی کردن مواد و تجهیزات پزشکی، انجام فعالیت های صنعتی را میتوان در این گروه قرار داد.
مخازن فشار بالا نوعی از مخزن تحت فشار هستند که در نوع خود بهترین هستند. در این مخازن، میزان فشار بالا است، و نسبت به خوردگی، دمای خیلی سرد و گرم و فشار خیلی زیاد مقاوم هستند. این مخازن در فشار بین 10000 تا 15000 کار میکنند و به طور معمول از استیل ضد زنگ ساخته شده اند. مواد به سرعت در این مخازن ترکیب شده و واکنش های شیمیایی با دقت بالایی صورت گرفته و میتوان راحت تر مواد شیمیایی حاصله را بدست آورد.
کاربرد انواع مخازن
از مخازن انبساط، در آبگرمکن های مسکونی استفاده میشود. این نوع مخازن فشار اضافی را جذب کرده تا گرما به راحتی منبسط شود. کاهش فشار باعث آسیب دیدگی لوله های مخزن میشود. فشار در این نوع مخازن لازم است که ثابت باقی بماند، در غیر این صورت منفجر خواهد شد. به همین دلیل لازم است که در بازه های زمانی کوتاه این نوع مخازن بازرسی شوند تا بتوان با کنترل شرایط، از وقوع حوادث ناگوار جلوگیری کرد.
از مخازن تحت فشار در ابعاد کوچک در دستگاه های تهویه هوا، عملیات واکنش های شیمیایی، دستگاه های تولید کننده برق، تولید مواد پتروشیمی و نفت، تخلیه فاضلاب و دستگاه های گرمایشی استفاده میشود. در این نوع کاربرد، گرما دفع شده و محل خنک میشود. مثال بارز این نوع دستگاه ها، کاهش گرمای در یک دستگاه است. گرمای حاصل از فعالیت یک برد الکترونیکی به بیرون منتقل شده و در نتیجه برد الکترونیکی خنک باقی میماند.
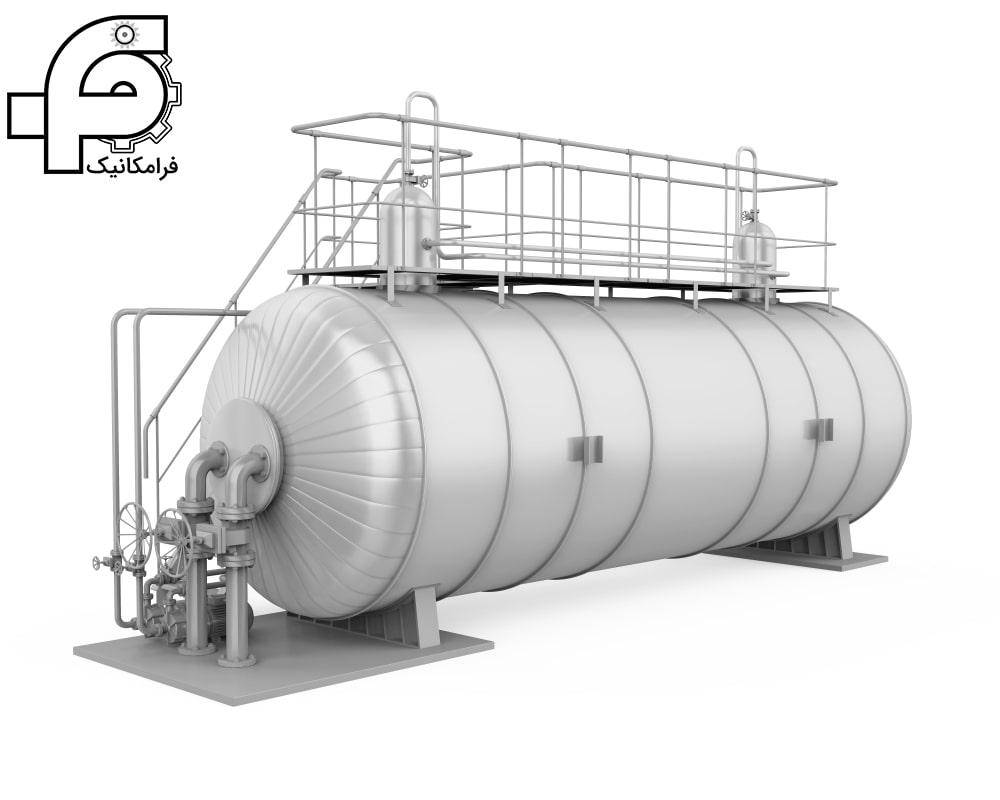
مخازن ذخیره و نگهداری
این مخازن، برای ذخیره و نگهداری مواد طراحی شده اند تا بتوان به محض نیاز به آن ها دسترسی داشت. از نمونه های بارز مخازن ذخیره میتوان به مخازن گاز پروپان، مخازن انواع گازها دیگر، مخازن آب گرم، و مخازن هوا اشاره کرد.
مخازن تحت فشار، در چاه های استخراج آب استفاده میشوند. میتوان به وسیله این مخازن، آب را از چاه بیرون کشیده و از طریق شیر آب استفاده کرد. همزمان با باز کردن شیر آب، فشار هوا مخزن، آب را با فشار به بیرون میراند. این کار آن قدر ادامه پیدا میکند تا فشار آن به دمای مشخصی افت کند که به طور معمول 40 تا 60 خواهد بود. در این فشار، پمپ آب شروع به کار میکند و آب را میتوان برای شست و شو و شرب استفاده کرد. همزمان با بسته شدن شیر آب، فشار دوباره به همان وضعیت قبل بر میگردد.
مخازن خلاء، برای تخلیه چاه های فاضلاب به کار میروند. مخازن فشار ASME یا همان آبگرمکن های ASME شناخته میشوند. این مخازن براساس استاندارد ASME ساخته شده اند. نشان ASME نشان میدهد که همه اصول و بازرسی ها در مورد این مخازن به اجرا در آمده است. همچنین مشخص میکند که این مخازن براساس اصول ایمنی ساخته شدهاند.
مخازن فشار نازک دیواره
مخازن فشار نازک دیواره، با ضخامت مشخصی طراحی شده اند. ضخامت دیواره چندان زیاد نیست. به شکل کروی یا استوانه ای طراحی و تولید میشوند. به طور معمول برای ذخیره و حمل مایعات و گازها به کار میرود. از این مخازن همچنین در صنعت هوا فضا استفاده میشود.
آبگرمکن ها برای گرم کردن آب استفاده میشوند. آب گرم شده برای پخت و پز، تولید برق، گرمایش محل، ضد عفونی کردن، استفاده میشود.
اجزای مخزن تحت فشار
مخازن تحت فشار با اجزایی شامل ظرف اصلی، اتصالات شیر اطمینان و درب مخزن تحت فشار شناخته میشوند. ظرف اصلی ممکن است به هر شکلی باشد. با این حال، معمولاً استوانه ای، کره یا مخروطی شکل است. این اشکال ساده بهتر از اشکال پیچیده تر کار میکنند و به راحتی میتوان آن ها را تعمیر کرد. نگهداری این دستگاه ها ساده و راحت است.
اجزای اضافی مخزن تحت فشار، به کار بهتر دستگاه ها کمک میکنند و هر چقدر که بیشتر و ساده تر باشند به همان اندازه کار دستگاه هم ساده تر خواهد بود. البته اجزای اضافی با تایید مهندسان نصب میشود. اگرچه وزن مخزن به طور یقین افزایش خواهد یافت، ولی این اجزای اضافی در برخی مواقع بنا به ضرورت و در برخی دیگر بنا به درخواست صنایع استفاده کننده نصب میشود.
شکل های اجزای اصلی مخازن تحت فشار
سه جزء در یک مخازن تحت فشار وجود دارد – پوسته، اتصالات و پایه. اجزای دیگر عمدتاً شامل نازل و هد هستند. مخزن های افقی به شکل مخروطی و کروی ساخته میشوند. پوسته اولین جزء مخزن تحت فشار است. به شکل های مختلف به مخزن جوش داده میشوند. به شکل کروی یا مخروطی شکل ساخته میشوند. هر چقدر که ضخامت پوسته بیشتر باشد به همان اندازه، ایمنی مخازن هم بالا خواهد بود. با اندازه گیری های مختلف میتوان ضخامت پوسته را مشخص کرد.
انتهای مخازن تحت فشار با هد مخزن بسته میشود. هدهای منحنی شکل، وزن کمتر، و استحکام بیشتری نسبت به هدهای مسطح دارند. هد نازل به شکل استوانه بوده و به راحتی داخل مخزن میشود. سر مخازن تحت فشار به شکل خمیده ساخته میشود. سرهای خمیده نسبت به مسطح، مقاوم هستند. میتوان داخل مخزن نیز از هد استفاده کرد و در نتیجه وضعیت دلخواه را داخل مخزن تحت فشار ایجاد میکند. نازل ها، به شکل استوانه ای ساخته میشوند. نازل ها برای هدایت جریان به داخل مخزن تحت فشار استفاده میشوند. همچنین برای استفاده در ابزارهایی مانند فشارسنج، ترموول، دستگاه های اندازه گیری مختلف به کار برده میشوند.
انواع پایه های مخازن تحت فشار
نگهدارنده ها، باعث ثابت باقی ماندن مخازن تحت فشار میشوند. در انواع مختلفی وجود دارند. در ساخت مخزن فشار از تکیه گاه هایی استفاده میشود که وزن را تحمل میکنند. به نگهداری مخزن تحت فشار در زلزله و طوفان های شدید کمک میکنند. نگهدارنده ها و تکیه گاه ها متناسب با اندازه و شکل مخزن ساخته میشوند. در این بخش از مخزن، هیچ فشاری وجود ندارد.
نگهدارنده ها به شکل های مختلف طراحی و ساخته میشوند. برخی نگهدارنده های برای مخزن تحت فشار افقی به کار برده میشوند. این نوع نگهدارنده ها از بروز فشار در برخی قسمت های مخزن جلوگیری میکنند. نگهدارنده های پایه ای برای مخازن کوچک به کار برده میشود. این نوع پایه ها، به مخزن جوش داده میشود.
صنایع کاربردی مخازن تحت فشار
در مخازن تحت فشار مواد مایع شیمیایی نیز نگهداری میشوند. در صنایع مختلفی مانند پالایش نفت، شیمیایی، برق، غذا و نوشیدنی و داروسازی استفاده میشوند. به طور کلی سه نوع اصلی مخزن تحت فشار وجود دارد که میتوان به مخزن تحت فشار به شکل های افقی، عمودی، کروی اشاره کرد.
با این حال، انواع خاصی از مخزن تحت فشار مانند برج خنک کننده، راکتورها وجود دارد که این نام ها تنها بر اساس کاربرد آنها ذکر شده است. متناسب با اندازه و وزن، پایه ها به مخزن جوش کاری میشود. این نوع پایه ها برای مخازن کروی و مخروطی و عمودی نیز به کار برده میشوند. گاهی مواقع نگهدارنده ها، به مخازن پیچ میشوند. نوع دیگری از نگهدارنده ها ، برای مخازن بلند عمودی استوانه ای به کار برده میشوند. این نوع نگهدارنده ها به بخش پایینی مخازن یا به بخش پایینی هد مخزن جوش کاری میشوند. وظیفه نگهدارنده جلوگیری از وارد آمدن فشار به مخزن است. ضخامت نگهدارنده ها مهم بوده و بنابراین با ورقه های ضخیم، نگهدارنده ها را میسازند تا مقاومت مخزن نیز افزایش یابد.
کاربرد مخازن تحت فشار
مخازن تحت فشار بیشتر اوقات، برای کاربردهای صنایع غذایی و آشامیدنی، شیمیایی، دارویی، پلاستیک و صنایع نفت و سوخت استفاده میشود. همچنین میتوان از آنها برای گرمایش و سرمایش استفاده کرد.
این مخزن تحت فشار برای نگهداری گازها و مایعات در فشارهای مختلف، کم یا زیاد، اما کاملاً متفاوت از شرایط محیط استفاده میشوند. سیلندرهای گاز فشرده، خلاء، تبرید یا مخازن آزمایشگاهی، نمونه هایی از مخزن تحت فشار به شمار میروند. اکثر مخزن تحت فشار برای مصارف صنعتی به کار برده میشوند. از کاربردهای دیگر میتوان به مخازن ذخیره آب گرم و مخزن هوای غواص های زیر آب اشاره کرد.
مخازن تحت فشار، مخازن تقطیر، و نگهداری گازهای مایع را در بر میگیرد. در صنعت، مخزن تحت فشار متناسب با نیاز و مواد ، به کار برده میشود.
صنایع همچنین میتوانند از آنها برای سرمایش و گرمایش استفاده کنند. از این مخازن در فراوری مواد استفاده میشود. با این مخازن میتوان مواد اولیه را تبدیل کرده و مواد شیمیایی مختلفی را تولید کرد.
مخازن تحت فشار، مناسب ذخیره و نگهداری گازها یا مایعات هستند. مدل های صنعتی مخزن تحت فشار مواد مختلف به روش های مختلف گرم میشوند.
هیترهایی که روی مخزن تحت فشار نصب میشوند با اتصالات فلنجی، جوشی یا رزوه ای به مخزن نصب میشوند. برای گرم کردن گازها و مایعات و تولید بخار میتوان از مخزن تحت فشار استفاده کرد.
روش های ساخت مخازن تحت فشار
مخازن تحت فشار با نقشه های مهندسی نرم افزار اتوکد و مطابق با الزامات دیگ بخار و ASME (انجمن مهندسی مکانیک آمریکا) طراحی و ساخته میشود. با روش هایی، میزان فشار مخازن به حداقل کاهش یافته و در نتیجه با ایمنی بیشتری کار میکنند.
راه حل هندسی برای به حداقل رساندن فشار وارده، طراحی و تولید مخزن تحت فشار کروی است. با این حال، این کار دشوار بوده و مقرون به صرفه نیست. بنابراین، ظرف به، شکل استوانه ای با سر محدب یا منحنی خواهد بود. اکثر این نوع مخازن با فولاد طراحی و تولید میشوند که از ایمنی لازم برخوردار هستند.
در ساخت مخزن تحت فشار از مواد مختلفی استفاده میشود. فولاد ضد زنگ یکی از رایج ترین مواد است، فولاد بهترین فلز برای ساخت مخازن به شمار میرود.
فلز فولاد در برابر خوردگی و زنگ زدگی و شرایط محیطی سخت و خشن نیز مقاوم است. با این وجود این فلز با روش های مختلفی آزمایش میشود تا میزان مقاومت کاملا مشخص شود. بخش طراحی و تولید با آزمایش های مختلف، میزان مقاومت فولاد را مشخص میکند.
در ساخت مخازن تحت فشار از فلز، و سایر مواد استفاده میشود. این بخش به تحمل فشار داخلی کمک میکند و از ظرف در برابر مواد شیمیایی محافظت کرده و از نشت مواد جلوگیری میکند. برای ساخت مخزن تحت فشار، چند استاندارد بین المللی وجود دارد که میتوان به انجمن مهندسین مکانیک آمریکا، هیئت ملی بازرسان مخزن و مخزن تحت فشار ، دستورالعمل تجهیزات مخزن فشار اتحادیه اروپا اشاره کرد. سازندگان مخزن تحت فشار بهتر است از یک یا چند مورد از این مجموعه مقررات در ساخت مخازن پیروی کنند.
جوشکاری در زیر دریا
برای ساخت مخازن تحت فشار از انواع مختلف جوشکاری استفاده میشود. جوش کاری و فشار روش های مناسبی برای اتصالات فلزات به هم دیگر به شمار میرود. جوش کاری در زیر دریا (SAW) با استفاده از الکترود به انجام میرسد که روشی کاملا مناسب است. بزرگترین مزیت SAW میزان رسوب بالای آن است. دقت جوشکاری بالا بوده و در مقایسه با سایر روش های جوشکاری، بسیار مقاوم تر خواهد بود.
جوشکاری با تنگستن (GTAW) روشی است که با استفاده از الکترود تنگستن، به انجام میرسد. این روش بیشتر برای جوش های دقیق و کوچک روی فولاد ضد زنگ و سایر مواد مانند آلومینیوم، منیزیم و آلیاژ مس استفاده میشود.
جوشکاری فلزی (GMAW) یا MIG یکی دیگر از فرآیندهای طراحی و تولید مخزن به شمار میرود. جوشکاری فلزی گاز با یک الکترود به انجام میرسد. با این روش میتوان پایه را به مخازن جوشکاری کرد. این روش دقیق انجام میشود. یکی از روش هایی است که در ساخت مخازن از آن استفاده میشود. در ساخت مخزن تحت فشار ، از MIG/GMAW و TIG/GTAW استفاده میشود.
مراحل ساخت مخازن تحت فشار
مخازن تحت فشار با روش کاملا متفاوتی طراحی و ساخته میشود. گالوانیزه کردن این مخازن باعث استحکام هر چه بیشتر آن ها خواهد شد. هر چقدر که این نوع مخازن، مقاوم طراحی و تولید شوند به همان اندازه میتوان از آن ها در بلند مدت استفاده کرد.
پس از آماده شدن فلزات، مخزن تحت فشار معمولاً با استفاده از یکی از سه فرآیند آهنگری، لحیم کاری و جوشکاری تولید میشوند. با هر یک از این روش ها میتوان فلزات را به یکدیگر متصل کرد، ولی در هر حال بازهم روش های منحصر به فردی وجود دارد که از آن ها هم استفاده میشود.
با آهنگری، لحیم کاری و جوشکاری میتوان قطعات فلزی را به هم متصل کرد. این روش ها باعث میشود تا قطعات فلزی کاملا بهم متصل شوند. هر چقدر که مخزن تحت فشار با اطمینان و استحکام بالایی طراحی و تولید شوند، به همان اندازه نسبت به خوردگی، پوسیدگی و عوامل و شرایط محیطی مقاوم خواهند بود.
طراحی و محاسبات مخزن تحت فشار
در طراحی و قبل از ساخت، مهندسان باید میزان فشار، دما، مواد، اندازه و شکل را تعیین کنند. میتوانند مخازن تحت فشار سفارشی را نیز تولید کرد. از آن جایی که این مخازن برای صنایع شیمیایی تولید میشوند لازم است که میزان مقاومت نسبت به مواد شیمیایی نیز درج شود. هر چقدر که اطلاعات دقیق و کامل باشد به همان اندازه صنایع استفاده کننده میتوانند با اطمینان بیشتری از آن ها استفاده کنند.
قوانین خاصی برای طراحی وجود دارد. موارد روش طراحی، توجه به وزن و فشار مجاز، ماده اولیه، و تولید در قوانین طراحی گنجانده میشوند. بازرسی نیز در بخشی از مجموعه طراحی مخزن فشار قرار دارد. توجه به میزان فشار مخزن یکی از مهم ترین مواردی است که به آن توجه میشود.
نحوه طراحی با هندسه و شکل مخزن ارتباط مستقیمی دارد. ضخامت لبه های دیواره های مخزن لازم است که محاسبه شود. با این روش میتوان از ایجاد بد شکلی مخزن جلوگیری کرده و از ایجاد فشار به مخزن اجتناب کرد. شکل مخزن، عاملی موثر بوده و در طراحی و تولید مدنظر گرفته میشود. باید از فشار بر مخزن جلوگیری کرد. هر چقدر که قوانین طراحی سختگیرانه باشد به همان اندازه مخازن تحت فشار نیز با استحکام بیشتری طراحی و تولید خواهد شد.
از قوانین انجمن ملی استانداردهای آمریکا (ASME) نیز بر ساخت مخازن تحت فشار استفاده میشود. موسسه نفت آمریکا (API) قوانین خاصی را برای مخازن تحت فشار که برای نگهداری نفت از آن ها استفاده میشود وضع کرده است.
قوانین طراحی و ساخت آبگرمکن ها نیز سخت گیرانه است. قوانین طراحی و ساخت این مخازن در هر کشوری متغیر خواهد بود ولی در هر حال، ایمنی این مخازن مهم بوده و لازم است که بازرسی ها نیز سخت گیرانه باشد.
تاثیر فشار داخلی و خارجی بر نحوه طراحی مخزن
برخی نیروها بر میزان فشار داخلی و خارجی مخازن تحت فشار تاثیر میگذارند. وزن مخزن، فشارهای خارجی، باد و زلزله بر طراحی و شکل و وزن مخازن تحت فشار تاثیر میگذارند. دما و فشار نیز بر طراحی تاثیر به سزایی دارد. ضخامت مخزن براساس این عوامل تعیین میشود. طراحی مخزن باید به نحوی انجام شود که عواملی مانند باد و زلزله بر کارایی و عملکرد آن تاثیری نداشته باشد.
انتخاب فلز برای ساخت مخزن براساس قوانین صورت میگیرد. در این مورد میتوان به مقرراتی که در این زمینه تهیه شده است رجوع کرد. مخزن لازم است به نحوی طراحی و ساخته شود که نسبت به خوردگی و فرسودگی مقاوم باشد.
میزان ضخامت دیواره مخزن براساس مقاومت فلز سنجیده میشود و دما در تعیین فشار مجاز وارده بر مخزن تاثیر به سزایی دارد. مشخصات فلز لازم است مورد توجه قرار گیرد تا در سرما یا گرما شدید، هیچ گونه اشکال یا ایرادی در مخزن به وجود نیاید.
متریال مورد استفاده در ساخت مخازن تحت فشار
قابلیت اطمینان مخازن تحت فشار به مواد مورد استفاده بستگی دارد. شش نوع مختلف از مواد در ساخت مخازن تحت فشار استفاده میشود. اولین فلز، تیتانیوم است که با ویژگی هایی مانند حفظ ساختار، مقاوم در برابر خوردگی، تعمیر و نگهداری ارزان، استحکام بالا، قابلیت ذوب بالا، سازگار با سایر فلزات، سازگاری با محیط زیست شناخته شده که برای طراحی و ساخت مخزن از آن استفاده میشود. امروزه تیتانیوم یکی از محبوب ترین فلزات در صنعت محسوب میشود.
از دیگر فلزاتی که برای ساخت مخزن فشار به کار برده میشود میتوان به آلیاژهای نیکل اشاره کرد که بخاطر ویژگی های مقاومت در برابر خوردگی، اکسیداسیون و قابلیت استفاده در محیط های سخت و خشن، مطمئن و بادوام بوده و یکی از بهترین فلزات شناخته میشود.
مخازن تحت فشار لازم است که محکم و مقاوم ساخته شوند. با فولاد ضد زنگ، میتوان این هدف را محقق کرد. این فلز در برابر مواد و واکنش های شیمیایی، و خوردگی، شرایط محیط، نور آفتاب، و حتی گرما یا سرمای بسیار شدید بسیار مقاوم است. فولاد ضد زنگ به راحتی با سایر فلزات جوش میخورد.
مخازن تحت فشار را میتوان با آلومینیوم نیز طراحی و تولید کرد. این فلز استحکام دارد. در مقایسه با فولاد ضد زنگ به راحتی یافت میشود و میتوان با دستگاه های صنعتی این فلز را تغییر داد. فلز آلومینیوم در مقایسه با سایر فلزات، به راحتی منبسط میشود.
کربن استیل از دیگر فلزات مناسب برای ساخت مخازن تحت فشار به شمار میرود. مقاومت این فلز بسیار بالا است. مقاومت کربن استیل منحصر به فرد و خاص است. به آسانی بازیابی میشود و نسبت به ضربات فیزیکی بسیار مقاوم است.
ماده هاستلوی
ماده هاستلوی برای طراحی و ساخت مخازن تحت فشار کاملا مناسب است و برای صنایع گاز، نفت، پتروشیمی و شیمیایی کاملا سازگار است. این ماده در برابر خوردگی و ترک خوردگی، و شکاف خوردگی کاملا مقاوم است. این ماده بادوام بوده و ماندگاری بالایی دارد. در انواع مختلفی مانند C276، S، C، B2 عرضه شده و به فروش میرسد.
تست ایمنی ساخت مخازن تحت فشار
بسیاری از مخازن تحت فشار باید مطابق با قوانین انجمن مهندسین مکانیک آمریکا (ASME) ساخته شده باشند و بر همین اساس به ثبت برسند. کد ASME و مخازن تحت فشار (ASME Section VIII Code) و استانداردها و کدهای بازرسی تعیین شده توسط سایر موسسات، مانند مؤسسه نفت آمریکا (API) به ایمنی هر چه بیشتر مخازن کمک میکنند. از آنجایی که این مخازن تحت فشار شدید قرار دارند، حتی کوچکترین نشتی میتواند باعث انفجار شود. با توجه به ماهیت پیچیده طراحی و ساخت مخازن تحت فشار، مقررات و استانداردهای متعددی برای اطمینان از ساخت و عملکرد ایمن مخازن تحت فشار وضع شده که میتوان به موارد زیر اشاره کرد.
- PD5500
- ASME VIII (بخش 1 و 2 به علاوه دارندگان نشان های استاندارد ASME U، U2، R و NB)
- EN13445
- EN14015 (BS2654)
- API 650
- API 6A
- 3
- قوانین DNV
- استانداردهای NORSOK
- استانداردهای GOST plus SNIP
- NACE MR0175/ISO 15156
- مطابقت با PED 97/23/EC
مهندسان همچنین ممکن است از فرمول های ریاضی، فیزیکی و شیمی در طراحی و ساخت مخازن تحت فشار استفاده کنند تا نسبت به مقاومت این نوع مخازن اطمینان حاصل کنند. اندازه و شکل و دمای مواد قابل نگهداری در این مخازن نیز از دیگر موضوعاتی است که در ساخت مخزن به آن ها توجه میشود.
تست مخازن تحت فشار
مخازن تحت فشار برای نگهداری گازهای سمی و خطرناک شیمیایی استفاده میشوند. بنابراین برخی مواقع انفجارهای خطرناکی نیز در محل هایی که این مخازن قرار دارند رخ میدهد. برای کاهش این نوع خطر، انواع تست برای این نوع مخازن به انجام میرسد. تکنیسین ها و اپراتورهای مجرب و متخصص این نوع تست را اجرا میکنند و بدین گونه میتوان اطمینان حاصل کرد که کار به درستی به انجام رسیده است. البته تست های دیگر پیشرفته ای نیز برای مخازن تحت فشار به انجام میرسد.
انواع تست مخازن تحت فشار
مخازن تحت فشار را با تست هایی آزمایش میکنند تا میزان مقاومت آن ها مشخص شود. یکی از این تست ها، تست بصری است. یک روش متداول تست، آزمایش بصری مخازن تحت فشار است. برای جلوگیری از خوردگی یا هرگونه آسیب فیزیکی قابل مشاهده استفاده میشود. تست بصری نیاز به نور خوب دارد. با روش تست بصری مخازن تحت فشار بازرسی میشود. با این حال، برخی از محل های مخازن تحت فشار میتوانند چالش برانگیز باشند. ذره بین های صنعتی با دقت بالا برای بررسی بصری سطح مخزن بهترین هستند. روش تست بصری را میتوان با استفاده از دوربین های فیلمبرداری دیجیتالی نیز انجام داد که دقت بالایی دارند و میتوان ترک خوردگی یا شکاف خوردگی را با این روش تشخیص داد.
تست ذرات مغناطیسی
تست ذرات مغناطیسی، یکی دیگر از تست هایی است که بر روی مخازن تحت فشار به انجام میرسد. یکی دیگر از تکنیک های تست ها که برای تشخیص ترک خوردگی و شکاف خوردگی استفاده میشود، آزمایش ذرات مغناطیسی است. فلز فولاد را با این روش آزمایش میکنند. این تکنیک ارزان است. آزمایش ذرات مغناطیسی برای تشخیص ترک هایی سطحی استفاده میشود. این تکنیک یک فرآیند دو مرحله ای است. ابتدا یک جریان مغناطیسی از قطعه عبور میکند. اگر ترک یا نقصی وجود داشته باشد، بلافاصله مشخص میشود. روشی دقیق بوده و میتوان در همه مکان ها از این روش استفاده کرد. با نور فلورسنت نیز میتوان ترک خوردگی و شکاف خوردگی را نیز تشخیص داد. چراغ قوه های با نور فلورسنت برای این کار کاملا مناسب هستند.
در آزمایش جریان الکتریسیته، یک کویل در نزدیکی سطح مخازن تحت فشار قرار میگیرد و جریان الکتریکی از آن عبور میکند. اگر نقصی در سطح مخازن تحت فشار وجود داشته باشد، مانع از جریان الکتریسیته میشود. با این حال، اگر مواد مخازن تحت فشار مانع جریان الکتریسیته شود، این آزمایش میتواند ترک خوردگی یا شکاف سطح بدنه را نشان دهد. این روش ارزان نبوده و البته در همه محل ها نمیتوان از آن استفاده کرد.
مخازن تحت فشار با تست نفوذ رنگ، نیز بررسی میشود. با اسپری کردن مایع روی سطح مخزن میتوان ترک خوردگی و شکاف خوردگی سطح مخزن را شناسایی کرد. با نور ماوراء بنفش و فلورسنت این کار راحت تر انجام میشود. از این روش ها امروزه استفاده میشود، ولی با این وجود مهندسین همواره به دنبال روش های جدیدی هستند تا بتوانند ترک خوردگی و شکاف خوردگی را در کوتاه ترین زمان ممکن تشخیص دهند.
آزمایش اولتراسونیک
برای تشخیص عیوب داخل مخازن تحت فشار از روش های زیر استفاده میشود. آزمایش اولتراسونیک یکی از آزمایش ها برای تشخیص عیب های مخزن به شمار میرود، بخاطر این که از امواج صوتی با فرکانس بالا برای تشخیص ترکیدگی استفاده میشود. امواج اولتراسونیک بر روی قسمت های ترک خورده سطح ارسال شده و ضخامت دیواره مشخص میشود. یک دستگاه اولتراسونیک امواج صوتی را برای تشخیص عیوب منتقل میکند. انجام خودکار این آزمایش بهترین روش برای استفاده است، بخاطر این که استفاده دستی، محدودیت هایی دارد و بنابراین بخاطر کند بودن بهتر است که از این روش استفاده نشود.
تست رادیوگرافی، آخرین تستی است که بر روی مخازن تحت فشار به انجام میرسد. با این تکنیک میتوان تغییرات مواد به کار برده در ساخت مخزن را متوجه شد. رادیوگرافی محبوب ترین روش است بخاطر این که میتواند عیوب مخزن فشار را ثبت کند و همچنین میتوان نتیجه آزمایش را نیز چاپ کرد. رادیوگرافی دیجیتال بهتر است، بخاطر این که میتوان در عرض چند ثانیه نتایج را بر روی صفحه نمایش کامپیوتر نمایش داد.
طراحی مخازن تحت فشار با استفاده از کد ASME Section Vill و نرم افزار PVElite
مقدمه
استانداردهای صنعت عموماً توسط نهادهایی نظیر انجمنهای حرفه ای ارگانهای تجاری و کمیته های فنی منتشر و بعد از آماده سازی توسط متخصصین به توافق صنایع میرسند. اساسا یک کد، استانداردی است که از لحاظ قانونی به تایید ارگانها و مراجع مربوطه رسیده باشد. به این ترتیب یک کد به معنی یک قانون مدون تلقی میشود و هدف هر کد تضمین امنیت عمومی و امنیت صنفی و فنی در یک فعالیت خاص میباشد. کدها معمولا توسط همان سازمانهایی تدوین میشوند که استانداردها را منتشر میکنند. برای مثال جامعه مهندسین مکانیک آمریکا (ASME) دارای یک برنامه جامع در زمینه تدوین استاندارها بوده و در عین حال هر ساله کد بویلر و مخازن تحت فشار (ASME Boiler and Pressure Vessel Code) را نیز ارائه میکند. حال با توجه به مطالب گفته شده با تعاریف زیر برای استاندارد و کد آشنا میشویم:
استانداردها (Standards)
اسنادی هستند که فقط یک سری پارامترهای طراحی را متذکر میشوند (recommends)
این پارامترها توسط یک گروه حرفه ای که شایستگی و تجربه لازم را دارند، تدوین شدهاند و به لحاظ حقوقی هیچ گونه مسئولیتی بر عهده آنها نمیباشد.
کدها (Codes)
کدها دسته ای از استانداردها هستند که برای، طراحی، ساخت، نصب و بازرسی محصولات اجباری میباشند. به عبارتی ساده تر کدها مرز بایدها و نبایدها هستند که محصول تولیدی را در صورتی که مطابق الزامات آنها باشد، ضمانت کنند (requirments).به این منظور برای کدها یک Ustamp تعریف میگردد که سازندگان باید آن را داشته باشند.
اسپک ها
در طراحی ممکن است از Specها نیز استفاده شود. یک Specification Spec مجموعه ای از استانداردها و کدها میباشد که توسط یک شرکت یا سازمان جمع آوری شده و در برخی موارد به مراتب سخت گیرانه تر از کد و استاندارد میباشد
در این قسمت با تعدادی از استانداردها و کلیات آنها آشنا میشویم.
- ANSI موسسه استانداردهای ملی آمریکا American National Standard Institute) تنها مکانیزم شناخته شده در ایالات متحده است که در تاسیس و تدوین استانداردهای آمریکا نقش دارد. در این مکانیزم هر استانداردی که قرار است ارائه شود باید در ANSI مورد بررسی قرار گیرد و سپس با تایید آن منتشر شود. البته تمام استانداردهای ایالات متحده توسط ANSI منتشر نمیشود و ASME، AISC، AWS و بسیاری از سازمانهای دیگر نیز کدها و استاندارهایی را در زمینه های مختلف منتشر میکنند
- AISC موسسه فولادسازی آمریکا (American Institute of Steel Construction)
- ASCE انجمن مهندسین سیویل آمریکا (American Society of Civil Engineering)
- ASTM انجمن تست و مواد آمریکا (American Society for Testing and Material تعداد زیادی استاندارد جهت طبقه بندی مواد مختلف ،مشخصات کارائی و روشهای تست آنها تالیف نموده است.
- ASME انجمن مهندسان مکانیک آمریکا (American Society of Mechanical Engineering)
- AWS انجمن جوشکاری آمریکا (American Welding Society)
- API موسسه نفت آمریکا (American Petroleum Institute)
- UBCکد بارگزاری سازهای آمریکا Uniform Building Code)
- BSI (BS) موسسه استانداردهای بریتانیا (British Standard Institute)
- DIN موسسه استانداردهای آلمان (Deutsches Institute fur Normung)
- EN استانداردهای اتحادیه اروپا (European UNION Standard)
- ISO استانداردهای سازمان بین المللی استاندارد International Organization for Standardization)
استانداردها و کدهای طراحی مخازن تحت فشار
استانداردها و کدهای مختلفی در زمینه طراحی مخازن تحت فشار وجود دارد. معادلات و روابط در این اسناد به صورت یک قاعده کلی تدوین شده است، به طوری که امروزه طراحان مخزن مبنای محاسباتشان این اسناد و قواعد ذکر شده در آنها میباشد. از مهمترین این کدها عبارتند از:
- ASME BOILER & PRESSURE VESSEL CODE
- BS 5500
- EN 13445
- AD merkblatt
این کدها شامل اطلاعات اساسی و فرمولهای مورد نیاز جهت طراحی مخازن تحت فشار میباشند
برخی از این اطلاعات عبارتند از:
- مشخصات و ویژگیهای مواد
- ابعاد قابل قبول برای اجزای تشکیل دهنده مخزن
- فشار و دمای طراحی
- الزامات مربوط به تحلیل تنشها عکس العمل ها و حرکات ناشی از فشار، دما و نیروهای خارجی
- الزامات مربوط به ساخت مونتاژ و نصب قسمت های مختلف مخزن
- الزامات مربوط به آزمایش بازرسی و تست مخزن
لازم به ذکر است که این الزامات انتخابی نیستند و باید به طور کامل اجرا شوند.
تاریخچه استاندارد مخازن تحت فشار و دیگهای بخار در آمریکا
با گذشت زمان و پیشرفتهای علمی و به بازار آمدن اولین ژنراتورهای بخار نیاز به یک استاندارد جهت طراحی مخازن تحت فشار بیشتر احساس شد. در طول قرنهای هجدهم و نوزدهم میلادی بخار به عنوان مهمترین منبع انرژی و عامل پیشرفت هر چه سریعتر انقلاب صنعتی در جهان شناخته میشد. ابتدای قرن بیستم شرایط به گونه ای بود که به طور متوسط در هر روز یک دیگ بخار منفجر میشد. در سال ۱۹۰۷ ، میلادی بعد از دو انفجار فاجعه آمیز در ایالات ماساچوست اولین قوانین مربوط به طراحی و ساخت دیگهای بخار در سه صفحه تدوین شد.
چهار سال بعد در ایالات و شهرهای دیگر آمریکا نیز قوانین مشابهی تدوین شدند. تدوین این قوانین باعث توجه بیشتر استفاده کنندگان و سازندگان به قوانین استاندارد جهت طراحی، ساخت و بازرسی دیگهای بخار گردید.
در سال ۱۹۱۱ انجمن مهندسین مکانیک آمریکا (ASME) کمیته ای متشکل از هفت نفر اصلی و هجده مشاور جهت استاندارد نمودن ساخت و بازرسی دیگهای بخار تشکیل داد. اعضای این کمیته تمام جوانب طراحی، ساخت، بازرسی نصب و راه اندازی دیگ های بخار را مورد مطالعه قرار دادند. نهایت در ۱۳ فوریه سال ۱۹۱۵ اولین کد با نام ASME Boiler Code انتشار یافت. در مدت زمان یازده سال شش استاندارد و در نهایت کد دیگر نیز منتشر شدند. اولین کد در زمینه مخازن تحت فشار در در سال ۱۹۲۵ انتشار یافت. این کد با نام “قوانین طراحی مخازن تحت فشار غیر آتشی” انتشار یافت و قسمت هشتم از مجموعه ASME بود که در زیر بر حسب تاریخ انتشار ارائه شده است.
قوانین طراحی مخازن تحت فشار غیر آتشی
- Section I – Boiler Construction Code, 1914
- Section III – Locomotive Boilers, 1921
- Section V – Miniature Boiler, 1922
- Section IV – Low Pressure Heating Boilers, 1923
- Section II – Material Specification, 1924
- Section VI – Rules for Inspection, 1924
- Section VIII- Unfired Pressure Vessels, 1925
- Section VII-Care and Use of Boilers, 1926
شرح قوانین
به دلیل عدم تکامل تکنولوژی جوشکاری، اولین استاندارد طراحی مخازن تحت فشار غیر آتشی (انتشار یافته توسط (ASME بیشتر بر روی ساخت مخازن با پیچ و پر متمرکز شده بود. همگام با گسترش استفاده از بخار، تکنولوژی جوشکاری نیز پیشرفت میکرد به طوری که در سال ۱۹۱۶ جوشکاری اکسی استیلن تا حد زیادی بهبود یافته بود و به مرور استفاده از مخازن تحت فشار دما بالای پرچی، در صنایع شیمیایی و مخصوصاً در صنایع نفت ناکارآمدی خود را در پروسه هایی نظیر شکست اتمی در صنایع پتروشیمی نشان میداد.
در پروسه شکست اتمی، با حرارت دادن نفت خام تحت فشار، آن را به گازوئیل تبدیل میکردند. فشار درون مخازن وابسته به پروسه از psi ۱0۰-۲۰۰۰ ( ۶۹۰-۱378 kPa) تغییر میکرد. در این فرآیندها جلوگیری از نشت مواد به خارج، در دمای بالا تقریبا غیر ممکن بود زیرا همواره از محل پرچها نشتی ایجاد میشد و در فرآیندهایی که سیکل گرمایش و سرمایش به طور مداوم وجود داشت این مشکل بحرانیتر بود اولین تلاش برای حل این مشکل جوشکاری قوسی لبه های اتصالات پرچ شده و اطراف پرچ ها بود. جوشکاری قوسی در آن زمان با استفاده از الکترودهای بدون روپوش انجام میشد که در نتیجه تماس مستقیم مذاب با هوا فلز ،جوش شامل اکسیدها و نیتریدهای زیادی بود و در نتیجه جوش حاصل غالبا سخت و ترد بوده و تحت شرایط کاری ترک میخورد.
تاثیر رشد جوشکاری بر قوانین
طبیعت ترد جوش های قوسی در آن زمان باعث جایگزینی آنها با جوش اکسی استیلن در مخازن اولیه شد. این فرآیند شامل گرم کردن لبه های ورق توسط شعله اکسی استیلن و سپس اتصال دادن دو سطح، بوسیله رسوب دادن الکترود به طور مستقیم به محل اتصال بود. این فرآیند باعث اتصال رضایت بخش ورقهای نازک میشد ولی این روش برای اتصال ورقهای ضخیم مناسب نبود زیرا در این ورقها به دلیل مشکلات ناشی از گرم نگه داشتن لبهها، جوشکاری به خوبی انجام نمیگرفت.
با پیشرفت جوشکاری قوسی و یافتن راههایی برای محافظت حوضچه جوش، استفاده از جوشکاری اکسی استیلن کاهش یافت. ایدهی اولیه برای حفاظت حوضچه جوش استفاده از روپوش بر روی الکترودها جهت دور کردن اکسیژن از حوضچه مذاب بود. در دهه بیست و سی میلادی مخازن بسیار زیادی با استفاده از جوشکاری ساخته شد ولی در آن زمان استاندارد ASME هنوز در مورد به رسمیت شناختن جوشکاری تردید داشت. به هر حال وقتی در استاندارد ASME استفاده از جوشکاری به رسمیت شناخته شد، قوانین وضع شده بسیار محتاطانه بود و ضرایب ایمنی بسیار بالا در نظر گرفته شده بود که عملا در صنایع کاربرد نداشت.
ادامه توضیحات قوانین
هنگامی که مراجع قانونی استفاده از استاندارد ASME را برای ساخت مخازن تحت فشار الزامی دانستند، بسیاری از مهندسین فعال در صنایع نفت و پتروشیمی با بخشهایی از استاندارد ASME مخالفت کردند زیرا با استناد به تجربیات آنها به کار بردن بسیاری از قسمتهای استاندارد ASME در صنایع پتروشیمی از ایمنی کافی برخوردار نبود و نیز استفاده از ضریب اطمینان ۵ که بالاترین ضریب ایمنی در آن زمان بین استانداردهای متداول بود برای بسیاری از موارد ضروری به نظر نمیرسید. همچنین عدم بیان تفاوتهای موجود بین فلسفه تدوین استاندارد ASME و استانداردهای API (موسسه نفت آمریکا) باعث تردید در مورد الزامات هر یک از استانداردها گردیده بود. با توجه به اجباری بودن استفاده از استاندارد ASME برای مخازن، API کمیته ای جهت تدوین نتایج تجربیات موسسه تشکیل داد.
مسیر پیوند دو استاندارد
بعد از تدوین اسناد و ارائه آن به موسسه استاندارد آمریکا پیشنهاد شد از این اسناد به عنوان استاندارد اجباری در صنعت پتروشیمی و نفت استفاده شود در نهایت جهت رفع آن اختلاف نظرها تصمیم بر آن شد تا کمیته ای از API و ASME تشکیل گردد و استانداردی تدوین شود که هر دو طرف آن را به رسیمت بشناسند. این پیشنهاد مورد استقبال دو طرف قرار گرفت و یک کمیته متشکل از API و ASME اولین ویرایش از API-ASME Unfired Pressure Vessel را در سال ۱۹۳۴ تدوین کرد. پس از ۱۷ سال هم چنان دو استاندارد جدا از هم جهت طراحی مخازن تحت فشار غیر آتشی وجود داشت.
- ASME فصل ۸ استاندارد مخازن تحت فشار غیر آتشی تحت نظارت ASME
- API-ASME فصل 8، استاندارد مخازن تحت فشار غیر آتشی تحت نظارت API
آخرین استاندارد API ASME در سال ۱۹۵۱ انتشار یافت در سال ۱۹۵۲ این دو استاندارد با هم تلفیق شده و با عنوان ASME Sec. VIII Unfired Pressure vessel انتشار یافت و تا سال ۱۹۶۸ تقریبا به همان صورت باقی ماند و سپس به ASME Section Vill Div1 (Rules of Construction of Pressure Vessel تغییر نام داده شد.
ASME Boiler & Pressure Vessel Code
این کد یکی از معروفترین و شناخته شده ترین کدها در زمینه طراحی مخازن تحت فشار انواع بویلرها و برجها در صنایع نفت و گاز، پتروشیمی، نیروگاهی و هسته ای میباشد. کمیته استاندارد ASME شامل چند کمیته فرعی است که هر کمیته فرعی شامل زیر گروههای متفاوتی میباشند. هر زیر گروه مسئول یک بخش خاص و نیز تکنیک های ویژه مربوط به ساخت در آن بخش میباشد کدهای ASME از سال ۱۹۲۰ تا به حال تغییرات زیادی کردهاند تا جوابگوی نیازهای صنعت باشند.
در حال حاضر هر سه سال یکبار ویرایش جدید کدهای ASME منتشر میشود. در هر سال نیز ضمیمه هایی که مبتنی بر تغییرات و توضیحات تکمیکی ویرایش قبلی میباشد، منتشر میگردد. برای طراحی مخازن تحت فشار و دیگ های بخار این کد دارای ۱۱ قسمت میباشد که در زیر بدان اشاره شده است از بین این ۱۱ قسمت، سه قسمت کاربرد بیشتری دارند که به اختصار با جزئیات آنها آشنا میشویم.
ASME Section II (Material Specification)
جهت دستیابی به اطلاعات مورد نیاز مواد مختلف جهت طراحی و ساخت مخازن تحت فشار میبایست به این بخش مراجعه نمود این بخش شامل اطلاعاتی نظیر مقادیر حداکثر تنش مجاز نمودارهای فشار خارجی مدول الاستیک، نسبت پواسون، خواص گرمایی و سایر پارامترهای مهم مواد میباشد و به چهار زیر مجموعه تقسیم میشود.
(خصوصیات مواد آهنی) Part A – Ferrous Material Specifications
(خصوصیات مواد غیر آهنی) Part B – Nonferrous Material Specifications
Part C – Specifications for Welding Rods, Electrodes, and Filler Metals
(یک دیکشنری کامل از مشخصات مکانیکی مواد مختلف) Part D – Properties
ASME Section IX (Welding and Brazing Qualifications)
این بخش مشخصات جوش و نیز فرآیندهای جوشکاری و بررسی کیفیت آن به منظور مطابق بودن با الزامات کد را در بر میگیرد. در واقع در این قسمت بعضی از مدارک مهندسی از جمله مدارک زیر که لازمه ساخت تجهیزات تحت فشار میباشند را میتوان تهیه نمود:
(WPS: Welding Procedure Specification): دستورالعمل انجام جوشکاری است که به جوشکار داده میشود تا بر اساس آن اقدام به جوشکاری نماید.
(POR (Procedure Qualification Record تایید دستورالعمل بالاست (WPS) و با استفاده از آن از استحکام جوش و کیفیت قطعه و دستگاههای جوشکاری اطمینان حاصل میشود. برای این مهم آزمایشاتی مانند تست های کشش، ضربه و خمش روی قطعه انجام میگیرد و نتایج آن در PQR ذکر میشود.
مطابق الزامات ASME Sec IX لازم است برای هر Category جوش یک WPS و PQR تعریف گردد. باید توجه داشت که تغییر برخی از پارامترهای ضروری مثل جنس، ضخامت و پروسه جوش موجب تغییر Category جوش میشود و تغییر سایر پارمترهای هندسی موجب تغییر در Category جوش نمیشوند.
ASME Section VIII (Rules for Construction of Pressure Vessels)
در این کد کلیه ی روابط و الزامات مورد نیاز جهت طراحی و ساخت مخازن تحت فشار ارائه میشود. این کد دارای سه بخش میباشد که در ادامه با هر یک از آنها آشنا میشویم.
ASME Section VIII Division 1 (Design by Rules) .)
در این بخش از کد، طراحی بر اساس یک سری قواعد و قوانین کلی انجام میشود و در مورد ترکیب انواع نیروها و تنش های ناشی از آنها (آنالیز تنش ها) صحبتی به میان نمیآید. در این قسمت از کد معیار مورد استفاده در ،طراحی ماکزیمم تنش نرمال با ضریب اطمینان 3.5 میباشد، لذا با استفاده از الزامات این قسمت المان ها نیاز به ضخامت های بیشتری دارند که این موضوع در مقایسه با استانداردهایی مانند DIN که دارای ضریب اطمینان ۲ میباشد، محسوس تر است.
دیدگاهتان را بنویسید