دستگاه تزریق پلاستیک
دستگاه تزریق پلاستیک چیست؟
آبا تا به حال به این فکر کردهاید که همه ی قطعات و محصولات پلاستیکی مورد استفاده روزمره ما از طریق تکنولوژی تزریق قالب پلاستیک و دستگاه تزریق پلاستیک (Plastic Injection Molding Machine) ساخته میشود. در واقع روش تزریق قالب پلاستیک یک نوع تکنولوژی ساخت و تولید انواع قطعات و محصولات پلاستیکی است، که درصد خطای بسیار پایینی دارد. بیشتر محصولاتی که طی مراحل ساختشان از پلاستیک استفاده شده، روش تزریق قالب پلاستیک به کار رفته است. در این روش، اول مواد اولیه ی پلیمری که به شکل گرانول میباشند، ذوب شده و بعد تحت فشار به داخل قالب تزریق میشوند. پلاستیک مایعی که درون قالب است خنک شده و به صورت جامد در میآید. مواد اولیه که در تزریق پلاستیک به کار میروند، پلیمرهای توموپلاستیکی میباشند، که قابل رنگ آمیزی کردن و پرشدن به وسیله افزودنی های دیگر است.
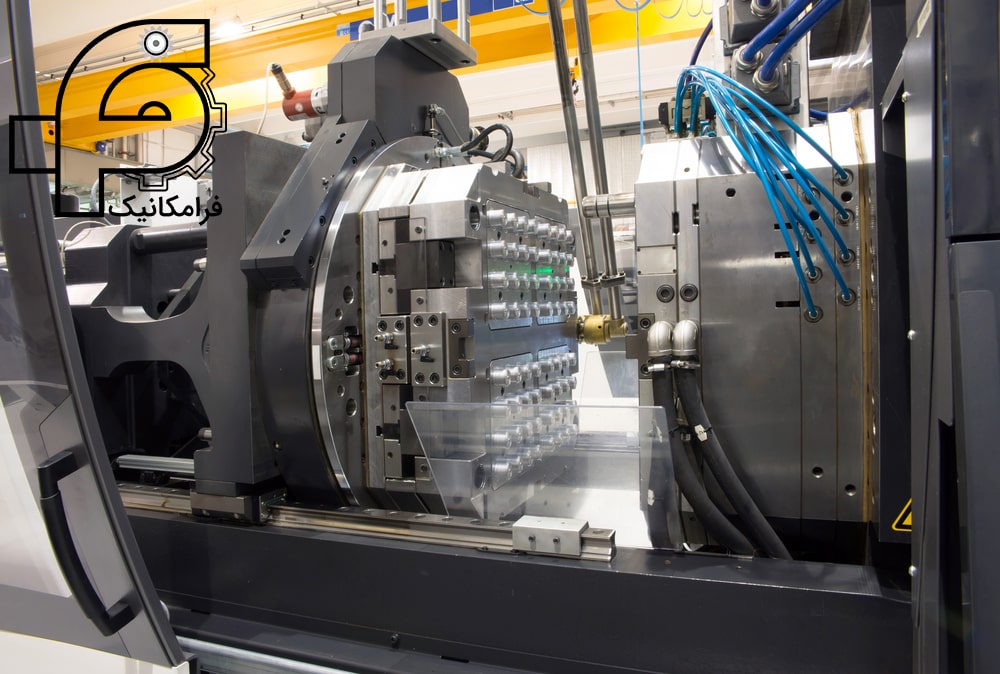
هزینه کم ساخت قطعات در تیراژهای بالا، موجب محبوبیت و گستردگی استفاده از دستگاه تزریق پلاستیک میشود. اما یکی از محدودیت های روش تزریق قالب پلاستیک عامل اقتصادی میباشد، زیرا با اینکه در تیراژ بالا از لحاظ اقتصادی به صرفه است، ولی برای شروع این پروسه به سرمایه اولیه زیادی نیاز است. محدودیت بعدی هم، زمان بالای رسیدن از مرحله طرح به مرحله تولید قطعات میباشد.
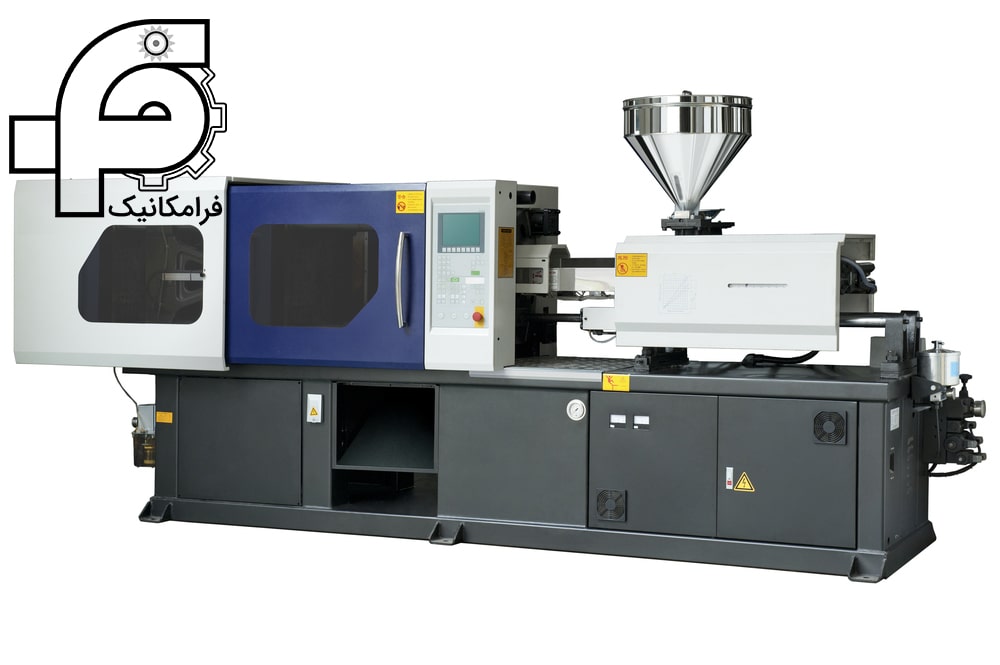
دستگاه تزریق پلاستیک چیست؟ و از چه قسمت هایی تشکیل شده است؟
دستگاه تزریق پلاستیک از دو قسمت تشکیل میشود. تزریق، قالب گیری. هر کدام از این دو نیز شامل چندین جزء هستند. بخش تزریق شامل قسمت های مارپیچی، نازل، بخش ورودی مواد اولیه، حرارت دهی و گرم کردن مواد اولیه است. در بخش قالب گیری هم مواد اولیه شکل نهایی خودشان را میگیرند و بعد از اینکه خنک شدند از قالب خارج میشوند.
دستگاه تزریق پلاستیک اجزای حساسی دارد که بر طبق اصول و شرایط خاصی کار میکنند. مثلا برای گرم کردن و ذوب پلاستیک ها و در مرحله بعدی ریتم سرد شدن آنها باید تنظیم دما با دقت انجام شود. این دستگاه دارای سایز، نوع و مدل های مختلف برای مشتریان است. با مطالعه دقیق در مورد تجهیزات و نحوهی عملکردشان به راحتی میتوانیم دستگاه مورد نظرمان را انتخاب کنیم.
از نظر طراحی، دستگاه تزریق پلاستیک بیشتر به شکل افقی ساخته میشود، اما بعضی از دستگاهها قابلیت تبدیل شدن به شکل عمودی را هم دارند. زمانی که به ادغام مراحل در ماشین آلات نیاز باشد، از این سیستم استفاده میشود.
تجهیزات دستگاه تزریق پلاستیک :
در تزریق قالب پلاستیک، تجهیزاتی از جمله دستگاه و قالب، همچنین واحدی برای کنترل دمای قالب لازم داریم. با کمک 3 عامل فشار و دما و سرعت، این قسمتها با هم در ارتباط هستند. بعد از اینکه مهندس یا طراح صنعتی یک قطعه را طراحی میکند، قالب ساز متناسب با آن قطعه قالب را میسازد. این قالب ها از جنس آلومینیوم یا فولاد ساخته میشوند، تا ویژگی های قطعه ای را که طراحی شده منعکس کنند.
اجزای اصلی دستگاه:
اجزای دستگاه تزریق پلاستیک عبارتند از: واحد تزریق، واحد گیره. واحد تزریق از بخش های موتور اسکرو، پیچ و بشکه رفت و برگشتی، بخاری، ترموکوپل، پیستون حلقه ای، ورق صفحه ای تشکیل شده. واحد گیره هم از بخش های قالب، گیره بیرونی موتور، میله های راهنما تشکیل شده است.
انواع دستگاه تزریق پلاستیک
در دستبه بندی دستگاه تزریق پلاستیک، عمدتا به وزن قطعه تولیدی و قدرت گیره توجه میشود. هر اندازه وزن قطعه تولیدی و قدرت گیره دستگاه بالاتر باشد، امکان تولید قطعات بزرگتر و سنگینتر را فراهم میآورد. المان های مهم در انتخاب و دسته بندی دستگاه تزریق پلاستیک عبارتند از:
- قدرت گیره
- ظرفیت واحد تزریق
- فاصله بین میله های راهنما
- کورس بازشو گیره
- حداقل و حداکثر ارتفاع قالب
ماشین های تزریق پلاستیک و اجزای آن
تجهیزات ماشین های تزریق پلاستیک
ماشین تزریق پلاستیک اجزای زیادی داشته و پیکربندی آن میتواند افقی یا عمودی باشد. بنابراین کلیه ماشین های تزریق پلاستیک دارای پنج سیستم کلی یا پنج قسمت اصلی میباشند:
- منبع نیرو
- قسمت تزریق
- قسمت مونتاژ
- قسمت نگهدارنده قالب
- سیستم کنترل
وظایف و قسمتهای مختلف ماشین تزریق پلاستیک
قسمت تزریق
دو قسمت تزریق امروزه به صورت گسترده در دستگاههای تزریق استفاده میشود. انواع قسمت تزریق عبارتند از:
- دستگاه با پیچ جلوبرنده تک/دو مرحله ای
- دستگاه با پیستون تزریق
دستگاه با پیچ جلوبرنده
دستگاه با پیچ جلوبرنده که عمومیت بیشتری این نوع سیستم تزریق برای مواد با ویسکوزیته بالا و وزن کم shot استفاده میشود.
این نوع ماشین نیز خود به دو نوع میباشد:
1- دستگاه با پیچ جلوبرنده ساده؛ سیستم مواد مذاب جمع شده در انتهای در اثر حرکت چرخشی پیچ برنده توسط اعمال نیروی فشاری به پیچ از طرف سیلندر تزریق مواد به داخل قالب تزریق میشوند
2- دستگاه با پیچ جلو برنده دو مرحله ای؛ در این نوع سیستم مواد مذاب جمع شده در انتهای سیلندر در اثر حرکت چرخشی پیچ جلوبرنده به درون یک سیلندر که ناظر تزریق به آن متصل است رانده میشود. با حرکت یک پیستون مواد مذاب به داخل قالب تزریق میشوند
این سیستم برای زمانهای چرخه تزریق کوتاه، انجام فرایند روان و به دست آوردن خواص فیزیکی بالا استفاده میشود.
دستگاه با پیستون تزریق
در این نوع سیستم مواد مذاب جمع شده در انتهای سیلندر در اثر حرکت پیستون تزریق در درون سیلندر مواد مذاب به داخل قالب تزریق میشوند. این سیستم میتواند برای مواد مختلف نظیر ترموپلاست آن تک سیلندر و برای مواد ترموست (دوجزئی) دو سیلندر باشند.
در شکل های زیر سیستم تزریق پیستونی برای مواد دو جزئی و سیستم تزریق پیچی را مشاهده میکنید
وظایف قسمت تزریق عبارتند از:
- بارگیری مواد
- گرم کردن و ذوب مواد
- انتقال مواد
- مخلوط و همگن کردن مواد
- تزریق مواد
- متراکم کردن مواد تزریقی
تزریق دارای قسمت های زیر میباشد
- قیف
- سیلندر
- هیتر
- پیچ جلو برنده
- شیر کنترلی
- نازل
- موتور الکتریکی یا هیدرولیکی
- جک تزریق
- ریل
- شیر کنترلی
شرح این قسمت ها
بخش اول این قسمت شامل قیف میباشد. قیف، ظرف بزرگی است که پلاستیک خام در آن ریخته میشود. ممکن است که مستقیماً به سیلندر متصل شود و یا از طریق محفظه تغذیه به سیلندر اتصال داده شود. انتهای قیف باز بوده و اجازه میدهد تا مواد به داخل سیلندر که دارای مکانیزمی برای گرم کردن و تزریق مواد است، وارد شود. این مکانیزم معمولاً دارای یک رام بیرون بر یا پیچ جلوبرنده است. این پیتزا جلوبرنده را ماردون مینامند.
امروزه در دستگاه ها اغلب از پیچ جلوبرنده استفاده میشود. پیچ جلوبرنده ممکن است توسط نیروی هیدرولیک یا موتور الکتریکی حرکت کند و چرخش آن باعث به جلو راندن مواد به صورت چرخشی و لغزشی میشود. مواد وارد شده به سیلندر توسط قیف با چرخش ماردون به جلو رانده میشوند. در حین حرکت مواد به جلو در اثر اصطکاک و حرارت اعمالی از اطراف ماردون مواد ذوب میشوند. مواد ذوب شده در انتهای سیلندر از طریق نازل با سرعت در اثر حرکت ماردون و فشار ایجاد شده به داخل قالب تزریق میشوند. افزایش فشار اجازه میدهد مواد فشرده شده و با نیرو به درون قالب وارد میشوند.
در هنگام تزریق، رینگ کنترلی روی سطح آب بندی رینگ سنتر کن نشسته و باعث مسدود شدن راه برگشت مواد به عقب میشود. در این حالت ماردون حکم بیستون را پیدا نموده و عمل تزریق انجام میشود. زمانی که مواد سرد و جامد شد، ماردون میتواند دوباره حرکت نموده و مواد را برای تزریق بعدی به جلو براند. ماردون دارای سه ناحیه اصلی ناحیه تغذیه یا بارگیری ناحیه گذر یا انتقال مواد از حالت جامد به خمیر تبدیل میشوند، ناحیه اختلاط میباشد. ناحیه گذر از نظر طولی تعادل نسبت طول سیلندر بوده و سایر نواحی هرکدام، یک چهارم طول سیلندر را به خود اختصاص میدهند.
پیچ جلوبرنده (پیچ حلزون)
فرم دندانها نسبت در طول پیچ متفاوت است. پیچ جلوبرنده یا پیش حلزون معمولا توخالی ساخته میشود تا جریان آب یا گاز آن را خنک کند چرا معمولا به شکل اژدر میسازند تا یکنواخت و همگن شدن محصول را افزایش دهد. شکل اژدر نسبت به مواد مختلف هندسه متغیری میتواند داشته باشد
وظایف پیچ جلوبرنده عبارتند از :
- بارگیری مواد گرانول
- انتقال مواد
- جمع کردن و ذوب مواد
- مخلوط و هم جدا کردن مواد
پیچ جلو برنده دارای مشخصات طراحی به شرح زیر است:
- پیچ جلو برنده از جنس فولاد خیلی سخت با سختی ۳۲۵ الی ۳۵۰ برینل (فولاد نیترید)، کروم اندود، نیتروژنه با صافی سطح بالا و گاهی مواقع با تفلون پوشش داده میشود
- معمولا نسبت طول به قطر D/L= آن ۱۰/ ۱۵/ ۲۰/ ۲۵/ ۳۵ میباشد
- دارای سه ناحیه ( بارگیری، متراکم سازی و اختلاط) است.
شیر کنترلی
وظیفه شیر کنترلی در دستگاه تزریق پلاستیک، ممانعت از برگشت مواد ذوب شده موجود در قسمت جلوی سیلندر به داخل ناحیه بارگیری در هنگام عمل تزریق است.
ناحیه گرم کردن
ناحیه گرم کردن به طور عمده روی سیلندر سوار است سیلندر از فولاد ریخته گری فولاد نیکل دار یا فولاد استیل ساخته میشود قرمز شده حرارت داده میشود و هر و با روش گریز از مرکز از مرکز آلیاژی متشکل از Ni، Crکروم، Co، Bo و با سختی ۶۲ راکول ( ضد سایش) پوشش داده میشود.
وظیفه ناحیه گرم کردن عبارتند از:
- ذوب کردن مواد پلاستیکی
- کنترل دما
توجه شود که حداکثر دما باید کمتر از ۵۰۰ درجه سانتی گراد باشد
چهار ناحیه گرمایی شامل سه ناحیه روی سیلندر و یک ناحیه در نازل داریم
انواع نازل
نازل باز
این نازل ها به راحتی تمیز میشوند میتوان به سرعت مواد یا رنگ را عوض نمود. برای ممانعت از افت دما قطر سوراخ نازل بایستی حداقل ۳ میلیمتر باشد، ناظر بایستی با زاویه سر پیچ جلو برنده یکسان باشد.
نازل بسته
این نازل با فشار مکانیکی مثل فنر و یا فشار هیدرولیکی کار میکند. نازل بسته امکان عکس العمل در هنگام ذوب مواد را دارد. انتقال حرارت بین ناظر و قالب را کاهش میدهد. این دو نازل برای زمانی که فشار پشت نسبتاً بالا نیاز است و جهت ممانعت از رشته شدن مواد به کار برده میشود. از معایب این نوع نازل افت فشار بالا نسبت به نازل باز است.
منحنی طول مسیر جریان دمای ذوب
برای مواد ترموپلاستیک طول مسیر جریان مواد مذاب و دمای مواد مذاب موثر است. طول مسیر جریان به دمای مذاب ضخامت دیواره قطعه سرعت تزریق و خواص مواد بستگی دارد. سرعت تزریق به توانایی دستگاه تزریق پلاستیک بستگی دارد.
قسمت گیره
قسمت گیره بایستی نیروی کافی برای مال نیروی قفل کن قالب در حین مرحله تزریق را داشته باشد. به عبارت دیگر اگر نیرویی قفل کن کافی نباشد، قالب از هم باز شده و مواد مذاب درخت جدایش به صورت پلیسه در خواهد آمد.
وظایف گیره
- تثبیت قالب و هدایت آن
- اعمال نیروی گیره
- تخلیه قطعه تزریق شده
قبل از تزریق پلاستیک مذاب به قالب، دو نیمه قالب، بایستی به واحد گیره بسته شود. وقتی که قالب به دستگاه تزریق وصل میشوند، هر کدام از دو کفشک قالب به صفحات بزرگی روی دستگاه تزریق بسته میشوند. کفشک یا صفحه جلوی قالب که حفره قالب به آنها متصل است، روی صفحه ثابت بسته شده و با نازل قسمت تزریق همراستا میشود. کفشک پشتی قالب که قسمت نری قالب روی آن سوار شده است به صفحه میانی متحرک بسته میشود. صفحه متحرک میانی روی چهار میله مهاری به عنوان راهنما حرکت میکند.
موتور گیره هیدرولیکی میله های گیره را به جلو رانده و باعث حرکت صفحه متحرک میانی به طرف صفحه ثابت میشود. وجود نیروی فشاری باعث میشود که قالب در حین زمان تزریق و خنک کاری بسته بماند. پس از طی شدن زمان لازم خنک کاری قالب توسط موتور گیره هیدرولیکی باز میشود. یک سیستم پران که به یک صفحه یا کفشک پشتی قالب متصل است، توسط میله های پرآن، قطعه را از حفره قالب بیرون میرانند.
قسمت گیره به سه حالت طراحی می شود
- نوع مفصلی
- نوع هیدرولیکی
- نوع هیدرو مکانیکی
گیره مفصلی خود در حالت ها و اشکال مختلفی طراحی میشوند. یک محرک انتهای بازوی مفصلی را به جلو حرکت داده و بازویی مفصل افزایش طول داده و صفحه متحرک حرکت میدهد. در ابتدای حرکت بازده مکانیکی پایین بوده و سرعت زیاد است و در انتهای کورس عکس این موضوع صادق است. بنابراین در گیرههای نوع مفصلی در نقاط مختلف سرعت و نیروی زیادی در چرخه تزریق خواهیم داشت. تحریک هم به صورت هیدرولیکی یا پیچی که توسط موتور الکتریکی حرکت داده میشود، انجام میشود.
مزایا و معایب تزریق پلاستیک چیست؟
مزایای تزریق پلاستیک عبارت است از:
- فرآیند قالب گیری بسیار سریع و کوتاه بوده، درنتیجه به سرعت و تعداد بالای تولیدات میانجامد.
- امکان استفاده از مواد پلاستیکی متنوع و انواع رنگی در این روش وجود دارد.
- تزریق قالب پلاستیک نیاز به نیروی کار کمتری دارد که باعث صرفه جویی در نیروی انسانی میشود.
- اتلاف مواد کمتر به علت استفاده از ضایعات پلاستیکی اضافی که بعد از قالب گیری تزریقی ایجاد میشود.
- کاهش عملیات تکمیلی پس از تزریق پلاستیک در تولید قطعات.
- کاربری بسیار آسان و راحت.
معایب تزریق پلاستیک عبارت است از:
- هزینه بالای طراحی اولیه و تولید قطعات با مقدار کم و مدت زمان طولانی.
- ماشین آلاتی که برای تزریق پلاستیک به آنها نیاز داریم گران هستند.
- رقابت زیادی در این عرصه وجود دارد و تولید زیاد است.
- به دلیل وجود فرآیند پیچیده در ساخت تزریق قالب پلاستیک و هزینه زیاد، قطعاتی که در دسته کوچک تولید میشوند هزینه بیشتری دارند.
محاسبه هزینه های دستگاه تزریق پلاستیک:
عواملی که در هزینه های روش تزریق قالب پلاستیک تأثیرگذارند عبارتند از: هزینه مواد اولیه استفاده شده در این فرآیند، که هر چقدر کیفیت درخواست سفارشات بالاتر باشد، قیمت نهایی هم بیشتر میشود. مورد بعدی هزینه ماشین کاری است، که با توجه به تیراژ محدود ماشین ها، جهت پایین آوردن قیمت قطعات، باید با تعداد تیراژهای بالاتری سفارشات انجام شود. در رابطه با هزینه های ساعتی نیز، نیروی انسانی و میزان ساعت کار ماشین ها مؤثر است. البته محل قرارگرفتن کارگاه و ابعاد قطعات مدنظر هم در قیمت نهایی تأثیر میگذارد. فاکتور آخر مؤثر بر هزینه های تزریق قالب پلاستیک هم طراحی قالب میباشد.
فرمول محاسبه هزینه ها:
فرمول کلی که برای محاسبه هزینه های روش تزریق قالب پلاستیک و درآوردن قیمت نهایی وجود دارد، فرمول زیر است:
هزینه مواد اولیه به اضافه ی هزینه ماشین کاری\تعداد قطعات، به اضافه ی هزینه های ساعتی\زمان تولید، مساوی میشود با هزینه هر قطعه
فرمول محاسبه هزینه های روش تزریق پلاستیک
هزینه هر قطعه = هزینه مواد اولیه + (هزینه ماشین کاری÷ تعداد قطعات) + (هزینه های ساعتی/ زمان تولید)
مکانیزم ساخت قالب تزریق پلاستیک:
مکانیزم طراحی و ساخت قالب تزریق پلاستیک از فعالیت های صنعتی محسوب میشود که برای انجام آن به بررسی سیستماتیک و اصولی نیازمندیم. با توجه به اینکه در کشور ما اکثر قالب سازی هایی که به صنایع کوچک مربوط هستند، از روش های طراحی سنتی استفاده میکنند، لزوم بهره مندی از فناوری های جدید در دستگاه تزریق قالب پلاستیک حس میشود. زیرا سخت افزارها و نرم افزارهای لازم در این زمینه وجود دارد، اما متأسفانه کمتر از آنها استفاده میشود.
در صنعت ماشین تزریق پلاستیک اگر در مسیر تکنولوژی گام برنداریم و با علم و دانش و فناوری مخالفت کنیم، در آینده ای نه چندان دور شاهد اختلافات بزرگی خواهیم بود و جبران خسارت این عقب افتادگی برایمان گران تمام خواهد شد.
بنابراین با بهره مندی از تکنولوژی تزریق قالب پلاستیک در یک زمان مشخص با صرف کردن هزینه ای کمتر، حداقل ضایعات تولیدی را داریم.
مکانیزم ساخت قالب ها به قرار زیر است:
تهیه نقشه و اسناد و مدارک، از مجری طرح تولید یا همان مشتری:
بعد از اینکه مرحله امکان سنجی در خصوص تجهیزات لازم برای ساخت قالب تزریق پلاستیک انجام شد، بر اساس قراردادی که با مشتری منعقد کرده ایم، همه ی اطلاعات درباره قطعه ای که قرار است تولید شود از جمله نقشه، مدارک فنی که به مواد اولیه مربوط است، محل قرارگیری قطعه و شرایطی که به کاربردش مرتبط است تست میشود، سپس کنترل کیفی قطعات دستگاه تزریق پلاستیک که به شکل مکتوب از مشتری گرفته شده انجام میگیرد، درنهایت توافقات لازم صورت میپذیرد.
تهیه نمودن نقشه سه بعدی از قطعه ای که در قرارداد تزریق پلاستیک ذکر شده و گرفتن تأییدیه از مشتری:
با توجه به بررسی کردن نقشه ها و مدارک، همچنین نمونه قطعه با استفاده از نرم افزار مکانیکال دسکتاپ، به تهیه نقشه های سه بعدی از قطعه مورد نظر پرداخته میشود. بعد از بررسی کامل و رفع مشکلات احتمالی، نقشه کامل شده و نهایی به تأیید کتبی مشتری خواهد رسید.
تهیه کردن و ارائه دادن چارت زمان بندی برای ساخت قالب تزریق پلاستیک:
برای طراحی کردن و ساختن قالب تزریق پلاستیک و کلیه مکانیزم هایی که به عملکرد قالب مرتبط است، زمان بندی مشخصی در نظر گرفته شده است. با بکارگیری از نرم افزارهای خاصی، عملیات کنترل نمودن پروژه به وسیله مدیر قالب سازی انجام شده و در موعد مقرر، عملیات ساختن قالب ها به اتمام میرسد.
طراحی کردن قالب تزریق پلاستیک و مکانیزم های عملکردشان:
این مرحله از اساسی ترین مراحل ساخت قالب تزریق پلاستیک به شمار میآید. در اغلب موارد، این مرحله به وسیله مدیر قالب سازی و بر مبنای تجربه و دانش موجود، همچنین وجود نمونه های مشابهی که از قبل ساخته شده اند انجام میشود. در این مرحله تجربه و دقت نظر برای کسب موفقیت حرف نهایی را میزند.
مدلینگ قالب تزریق پلاستیک در سیستم کامپیوتر که به شکل کامل و تفکیکی است:
بعد از اینکه مرحله طراحی قالب تزریق پلاستیک را با کمک نرم افزارها پشت سر گذاشتیم، مدلینگ تمامی قسمت های قالب تزریق پلاستیک به شکل کامل و تفکیکی انجام میشود و قالبی که ساخته شده برای بررسی شدن فرآیند تولید قطعه آماده میشود.
تحلیل کردن فرآیند تولید شدن قطعه در قالب تزریق پلاستیک:
بعد از اینکه مدلینگ در خصوص بخش های مختلف قالب و همچنین مونتاژ قالب تزریق پلاستیک انجام شد، تولید قطعه مورد نظر و چگونگی پر شدن حفره های موجود در قالب با استفاده از نرم افزار، تجزیه و تحلیل میشود. سپس شرایط تولید در یک ماشین تزریق پلاستیک و تمامی خطرات احتمالی مثل وجود هوا و تزریق ناقص، از همه مهم تر توزیع حرارت در قسمت های مختلف قطعه در زمان تولید، توسط نرم افزار مورد بررسی قرار گرفته و اصلاح میشود.
مرور کردن طراحی مدل ساخته شده و همچنین مکانیزم های عملکرد قالب تزریق پلاستیک:
آخرین مرحله ای که قبل از ساختن قالب تزریق پلاستیک در کارگاه میباشد، مرور کردن طراحی مدل ساخته شده و همچنین مکانیزم های عملکرد قالب با کامپیوتر است. این کار معمولا به وسیله مدیر قالب سازی انجام میشود و در نهایت اصلاحات احتمالی در قالب لحاظ میشود.
تهیه ی مواد اولیه با متریال فولاد جهت ساخت قالب تزریق پلاستیک:
برای اینکه کیفیت کار بالا برود و قالب تزریق پلاستیک از دوام و عملکرد خوبی هم برخوردار باشد، از فولادهای شناسنامه دار استفاده میشود. اینگونه فولاد دارای سختی مناسبی میباشد و علاوه بر اینکه خوش تراش است، از قابلیت پولیش کاری با پوشش بالایی برخوردار است. این دسته از فولاد ها به خاطر آبکاری خاصشان پس از ساخت قالب، غیر از آبکاری های ضد سایشی هیچ نیازی به آبکاری سخت ندارند.
ساخت بخش های مختلف قالب تزریق پلاستیک با استفاده از دستگاه CNC:
کلیه مراحل ساخت بخش های مختلف قالب تزریق پلاستیک و مدلهایی که به عملیات اسپارک مربوط است، با استفاده از نرم افزار های Edge Cam و Power Mill و به وسیله دستگاه CNC انجام میشود. کاربرد مجموعه ای از عوامل ذکرشده، علاوه براینکه باعث افزایش سرعت ماشین کاری میشود، باعث کنترل دقیق تر ساخت و حذف کردن خطاهای احتمالی اپراتور میشود. در ضمن بدون استفاده از این سیستم های نرم افزاری در دستگاه تزریق پلاستیک، امکان ساخت قالبهای پیچیده وجود نخواهد داشت.
مرحله تکمیلی ساختن قالب تزریق پلاستیک در کارگاه:
این مرحله، اسپارک کاری قالبی است که در حال ساخت بوده و تمام فعالیت ها، با ماشین های ابزاری که در صنعت متداول هستند و به وسیله اپراتورهای ماشین انجام میشود، صورت میپذیرد.
تست قالب تزریق پلاستیک ساخته شده به وسیله جریان پارافین:
بعد از مراحل ساخت و مونتاژ شدن بخشهای مختلف قالب تزریق پلاستیک به جهت آب بندی بهتر قالب توسط دستگاه تست و با استفاده کردن از جریان پارافین، بخشهای سمبه و ماتریس کنترل میشود. البته ذکر این نکته لازم است که از دستگاه تزریق پلاستیک به تعداد خیلی کم و محدود در صنعت خودرو سازی وجود دارد.
آبکاری کردن و سخت کاری نهایی قالب ها:
آخرین مرحله در ساخت قالب تزریق پلاستیک و همچنین آبکاری و سخت کاری، مربوط به بخشهای متحرک قالب است. انجام این مرحله معمولا بعد از تولید آزمایشی بوده که تأیید کتبی مشتری انجام شده است.
طرز کار دستگاه تزریق پلاستیک:
طرز کار دستگاه تزریق پلاستیک شامل 7 مرحله میباشد:
مراحل و نحوه کار دستگاه تزریق پلاستیک:
مرحله بستن یا Clamping:
این مرحله قسمتی از دستگاه تزریق پلاستیک است که زمان پروسه تزریق، قالب را به شکل بسته نگه میدارد و بعد از اینکه عملیات انجام شد آن را باز میکند. به دلیل اینکه قالب ها از دو نیمه تشکیل شده اند که در زمان تزریق باید به وسیله Clamping در کنار هم ثابت شوند.
مرحله تزریق، یا ترکیب شدن گرانول ها با مواد افزودنی:
در این مرحله مواد پلاستیکی که عموما به صورت گرانول های پلیمری و دانه دانه هستند، خشک میشوند و از بالا وارد قیف دستگاه تزریق پلاستیک شده و پس از عبور از سیلندری که به وسیله هیترها احاطه شده، گرم میشوند و به حالت رزین تبدیل میگردند. مواد گرانولی توسط مارپیچی زیر و رو شده و با پودر ها و پیگمنت های رنگی و دیگر مواد افزودنی ترکیب میشوند. مواد که با چرخش مارپیچ در قسمت جلویی ذخیره شدند، عملیات تزریق انجام میگیرد و مواد به راهگاه قالب تزریق پلاستیک وارد میشوند. شدت فشار وارده به مارپیچ به قطر نازل بستگی دارد. در بعضی از دستگاه های تزریق پلاستیک از پیستون منگنه ای به جای مارپیچ استفاده میگردد.
مرحله مسکن Dwelling:
در این مرحله به عنوان یک مسکن در فرآیند تزریق پلاستیک عمل میکند تا کارها به خوبی صورت پذیرد. به این جهت که با مکثی که انجام میشود، مواد مذاب داخل کویتی ها، به طور کامل پر شده و باید گازهایی که طی این مراحل ایجاد شده از طریق فضاهایی که در دستگاه تعبیه شده اند خارج بشوند.
خنک کاری یا Cooling:
در این مرحله برای اینکه قالب ها به آسانی بتوانند از دستگاه تزریق پلاستیک خارج شوند، باید به شکل جامد تبدیل شوند. به این ترتیب مواد مذاب خنک شده، وقتی به حالت جامد درآمد، آماده خروج از دستگاه تزریق پلاستیک است. اگر غیر از این حالت باشد محصولتان به شکل قالب در نیامده و تغییر شکل زیادی پیدا میکند.
مرحله باز شدن قالب تزریق پلاستیک یا Mold opening:
در این مرحله برای اینکه قالب ها آماده بیرون افتادن شوند، Clamping باز میشود. بنابراین دو نیمه قالب ها از یکدیگر باز شده و به بیرون انداختن قالب کمک میکنند.
Ejection یا بیرون اندازی:
برای این عملیات چند میله همراه با یک صفحه برای خارج کردن قطعه ی ساخته شده از دستگاه تزریق پلاستیک به کار گرفته میشود. قطعه ی ساخته شده نهایی به صورت کامل تمیز میگردد. رانرهای قطعه و مواد اضافی که زائد هستند و مورد استفاده نمیباشند از قطعه مورد نظر جدا و تمیز شده، که از این مواد اضافه در فرآیندهای بعدی و برای تزریق پلاستیک در قالب های دیگر، مجددا استفاده میشود.
مواد اولیه تزریق پلاستیک:
پلیمرها به دلیل تنوع زیادی که دارند به محبوب ترین مواد اولیه که در تزریق پلاستیک استفاده میشوند، تبدیل شده اند.
پرکاربردترین مواد اولیه در تزریق قالب پلاستیک عبارتند از:
ABS:
این پلیمر همانند پلی کربنات، در برابر گرما مقاوم بوده و ضد ضربه است. البته ABS در برخورد با مواد شیمیایی آسیب پذیر است. بیشترین کاربردش به عنوان مواد اولیه تزریق قالب پلاستیک در ساخت انواع قطعات الکترونیکی مانند آداپتورهای شارژر، کلیدهای کیبورد، محافظ های پلاستیکی سوکت، محفظه های لوازم برقی است. همچنین ساخت و تولید لوازم یدکی خودرو نیز از دیگر موارد پرکاربرد این پلیمر میباشد.
PEI:
نوعی از پلیمر ترموپلاستیک است که دارای عملکرد بالایی است و مقاومت زیادی در برابر آتش سوزی و گرما دارد. در صنایع پزشکی و هوافضا کاربرد فراوانی دارد. البته تهیه ی این نوع پلیمر برای تزریق پلاستیک هزینه ی زیادی دارد.
Nylon:
یکی دیگر از مواد اولیه که در تزریق پلاستیک کاربرد دارد، نایلون ها هستند که از خانواده ی پلیمرها محسوب میشوند. نایلون ها دارای استحکام بالایی بوده و مقاومت شیمیایی خوبی دارند و بهترین جاذب رطوبت هستند. از نایلون ها برای ساخت انواع چرخ دنده های پلاستیکی و نیز ساخت لوازم خودرو استفاده میشود.
PEEK:
پلیمر PEEK شباهت زیادی به پلیمرهای PEI دارد. البته تفاوتش با PEI در این است که به جای اینکه در برابر گرما و آتش سوزی مقاوم باشد، دارای خواص مکانیکی بسیار بالا و مطلوبی است. PEEK هم در صنایع هوا فضا و پزشکی از مواد اولیه ای است که کاربرد زیادی دارد.
Polyethylene High Density:
این پلیمر با نام اختصاری HDPE شناخته میشود. HDPE قابلیت مقاومت زیادی در مقابل ضربه دارد و به همین علت میتوان جزئیات دقیقی را بر رویش پیاده سازی نمود. هرچند که این پلیمر از استحکام چندان زیادی برخوردار نبوده و معمولا برای ساخت لوازم مصرفی مورد استفاده قرار میگیرد.
Delrin:
مواد اولیه ی دیگری که در تزریق پلاستیک از آن استفاده می شود، درلین نام دارد. درلین در هنگام تزریق میتواند تاب بردارد. به علت خاصیت خود روان کنندگی و استحکام و سختی زیادی که دارد، در تولید قطعات مکانیکی و محصولات پلاستیکی منزل کاربرد دارد.
Polycarbonate:
این نوع پلیمر مقاومت بسیار زیادی در برابر گرما و ضربات شدید دارد. با این وجود که پلی کربنات برای ترک برداشتن مستعد است، اما در ساخت انواع لوازم مصرفی مانند چراغ اتومبیل و سی دی از آن استفاده میگردد.
Polystyrened:
یک نوع ارزان از ترموپلاستیک ها، پلی استایرن ها میباشند که به مواد غذایی واکنشی نشان نداده، به همین علت هم آنها را در ساخت انواع ظروف پلاستیکی مورد استفاده در آشپزخانه به کار میبرند.
Polypropylene:
پلیمر پلی پرولین مقاومت شیمیایی بالایی دارد و به همین دلیل از آن مانند پلی استایرن برای ساخت لوازم خانگی، همچنین انواع لوازم بسته بندی استفاده میشود.
کاربردهای دستگاه تزریق پلاستیک در صنایع مختلف:
همه ی ما اگر به اطرافمان نگاهی بیاندازیم حتما با یک جسم پلاستیکی مواجه خواهیم شد. این جسم به احتمال خیلی زیاد به وسیله دستگاه تزریق پلاستیک تولید شده است. به طور کلی استفاده از این دستگاه ها کاربردهای زیادی دارد که در انواع صنایع در زمینه ی تولید قطعات از آنها بهره میبرند.
صنایعی که از دستگاه استفاده میکنند:
صنعت هوا فضا، خودرو سازی، تولید قطعات پلاستیکی از انواع تجهیزات پزشکی تا اسباب بازی، صنایع کشاورزی و باغبانی، صنایع نظامی، صنایع ارتباطی، راه سازی و شهر سازی، آب و فاضلاب و … همگی در ساخت قطعات پلاستیکی خود از دستگاه تزریق پلاستیک استفاده میکنند. قطعاتی که از جنس پلیمرهای گوناگون میباشند، زیرا هر کدام از پلیمرهایی که به عنوان مواد اولیه قطعات پلاستیکی به کار گرفته میشوند، دارای ماهیت های شیمیایی مختلف و خواص متفاوتی هستند.
امروزه با توسعه و رشد سریع صنعت پلاستیک سازی و کاربرد این دسته از محصولات در صنایع هوا فضا و هوانوردی، ماشین آلات و الکترونیک، خودرو سازی و صنایع دریایی، نیاز به قالب ها هم افزایش چشمگیری یافته است. برای طراحی انواع قالب ها، دیگر روش های سنتی جوابگوی نیازها نیستند.
در ادامه با بخشی از کاربردهای دستگاه تزریق پلاستیک در صنایع مختلف آشنا میشویم.
کاربردهای مهم این تکنولوژی در صنایع مختلف:
صنعت ظروف پلاستیکی:
کاربرد ماشین آلات تزریق قالب پلاستیک در تولید اجزای کوچکی مثل درب بطری تا سینی هایی که در شام های تلویزیونی مورد استفاده است، همچنین صنایع بسته بندی و نیز صنعت نوشیدنی و غذا میباشد.
صنعت خودرو سازی:
انواع قطعاتی که در خودروهای مدرن وجود دارند از عناصر تزریق قالب پلاستیک هستند. مانند داشبورد، ضربه گیرها، حتی قطعات کوچکتری مثل جا لیوانی، محفظه ی آینه ها و … . پس استفاده از دستگاه تزریق پلاستیک جزو ضروی ترین ماشین آلات است.
صنعت پزشکی:
محصولات پزشکی معمولا باید ضد ضربه و نشکن بوده، البته دارای کیفیت بالایی هم باشند. به همین جهت دستگاه تزریق قالب پلاستیک برای تولید تجهیزات پزشکی و دارویی بسیار مهم و حیاتی است. از این رو انواع قطعات پزشکی و دارویی از بطری های قرص گرفته تا اجزای اشعه ایکس همگی نیازمند به صنعت ماشین آلات تزریق پلاستیک هستند.
صنعت کشاورزی و باغبانی:
امروزه استفاده از پلاستیک تقویت شده، به دلیل ویژگی های مهمی که دارد ازجمله مقاومت در برابر اشعه ماوراء بنفش، مقاومت در مقابل رطوبت، مقاومت در برابر انواع ضربه و توانایی ایجاد محصولاتی که در کشاورزی بادوام اند، مورد توجه شدیدی در صنعت کشاورزی در جهت استفاده از دستگاه تزریق پلاستیک، قرار گرفته است.
صنعت اسباب بازی:
استفاده از دستگاه تزریق پلاستیک بخاطر وزن سبک، رنگارنگی، پیاده کردن جزئیات ظریف در قالب ها، تولید سریع، قدرت و سازگاری با محیط زیست از دلایل کاربرد دستگاه تزریق پلاستیک در صنعت اسباب بازی است.
صنایع نظامی:
تزریق قالب پلاستیک این امکان را دارد که مایل بیشتری را طی کرده و یکنواختی را تضمین کند. همینطور به دلیل کاهش وزن تمام شده با پلاستیک و دوام بالا کاربرد زیادی در صنایع نظامی دارد.
صنایع هوایی:
برای ساخت قطعات مختلف هواپیما که بتوانند در شرایط سخت دوام بیاورند از قالب گیری تزریقی استفاده میشود. برخی از این قطعات که توسط دستگاه تزریق پلاستیک تولید شده اند، شامل پره های توربین، پانل ها، حاشیه ها، لنزها، محفظه های توربین، محفظه و ظروف، اجزای شاسی میباشند.
صنعت شهرسازی و راه سازی:
استفاده از دستگاه تزریق پلاستیک در این صنعت از لوله های پلاستیکی گرفته تا پیچ ها و قطعات بزرگتری که در دکوراسیون، کفپوش، سیم کشی، پوشش های دیوار و … از مواد پلاستیکی استفاده میشود.
چگونه از بروز مشکلات در قالبگیری پیشگیری نماییم؟
با وجود اینکه استفاده از دستگاه تزریق پلاستیک کار تولید کنندگان را راحت کرده، اما هنوز هم شاهد بروز مشکلاتی هستیم که به شکل های گوناگون بر روی محصولات نهایی تأثیر گذارند. با شناسایی این قبیل مشکلات و دلایل به وجود آمدنشان میتوان جلوی این اتفاقات را تا حد زیادی گرفت.
در فرآیند تزریق پلاستیک انواع مشکلات به صورت های مختلف بروز میکنند که بهترین راه برای جلوگیری کردن از آنها عیب یابی به موقع است.
مراحل عیب یابی در فرآیند تزریق پلاستیک:
در این خصوص ابتدا باید پیش از شروع پروسه تزریق عیب یابی انجام شود. به این صورت که رطوبتی که در مواد پلاستیکی موجود است رفع شود. دمای قالب و دمای مواد مذاب به درستی تنظیم شود. از سلامت دستگاه تزریق پلاستیک اطمینان حاصل شود. در صورت لزوم در پارامترهای گوناگون فرآیند، تغییرات لازم انجام بگیرد.
در صورت بروز مشکلات در هر کدام از پارامترهای فرآیند تزریق پلاستیک، در محصولات نهایی نیز مشکلات گوناگونی به وجود میآید. به این ترتیب لزوم عیب یابی و آگاهی از بروز مشکلات در فرآیند تزریق پلاستیک، میتواند کمک شایانی در جلوگیری از مشکلات دستگاه تزریق پلاستیک کند و باعث عرضه محصولات با کیفیت به بازار شود.
دیدگاهتان را بنویسید