دایکاست یا ریخته گری تحت فشار
آشنایی با ریخته گری دایکاست و کاربرد آن
تولید قطعات نازک با استحکام بالا با روش ریخته گری؛ تنها توسط دایکاست یا دستگاه ریخته گری تحت فشار (دایکست) امکان پذیر است.
در حالی که توانایی کاهش وزن فیزیکی، عامل اصلی افزایش تقاضا برای آلومینیوم و سایر قطعات آلیاژی سبک در سالهای اخیر بوده است، خواصی از جمله هدایت الکتریکی و حرارتی، استقامت مکانیکی، خوردگی و مقاومت بدنه، توجه تولیدکنندگان را در بسیاری از موارد به خود جلب کرده است.
با توجه به این ویژگی های منحصر به فرد، فلز سبک میتواند برای ریخته گری اجزای پیچیده و حیاتی ایمنی در خودرو، الکترونیک و هوافضا استفاده شود. همچنین یک گزینه تولید مقرون به صرفه برای تولید قطعات ساده از اجزای روشنایی گرفته تا ابزار آشپزخانه ارائه میدهد.
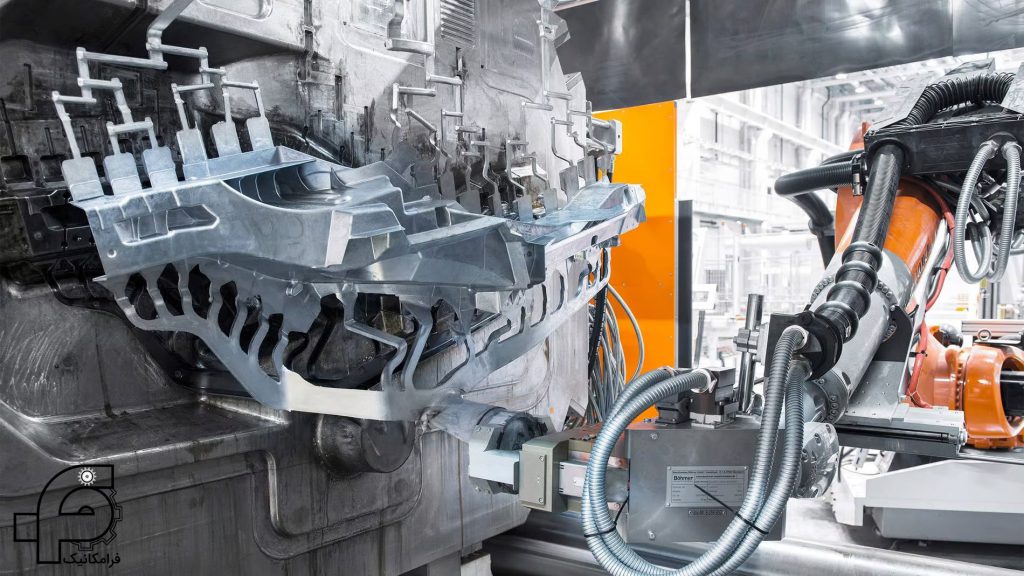
ریخته گری چیست؟
متداولترین روش و قدیمیترین فرآیند ساخت و تولید، قطعات فلزی در صنایع مختلف است که با ذوب مواد و ریختن آنها به درون قالب انجام میگیرد. مبنای فرآیند ریخته گری، تولید بر حسب ذوب، انجماد و شکل گیری ماده مذاب درون قالب از پیش طراحی شده، است.
تعریف دایکاست چیست؟
به نوعی از فرآیند تولیدی که از روش ریخته گری با اعمال فشار برای هدایت مواد مذاب و تزریق به درون قالب استفاده کند، دایکست (دایکاست) میگوییم. شکل پذیری و سرد و سخت شدن قطعه نیز درون قالب صورت میگیرد تا قطعات شکل مورد نظر را پیدا کنند. اعمال فشار برای حذف مک ها و تخلخل ها و درنتیجه افزایش استحکام قطعات میباشد.
دایکاست یک فرآیند ریخته گری فلز است که اغلب برای ایجاد قطعات با کیفیت بالا و بادوام برای استفاده در کاربردهای مختلف استفاده میشود. اگر به دنبال فرآیند تولیدی هستید که بتواند قطعات فلزی با کیفیت بالا تولید کند، ریخته گری دایکست میتواند انتخاب مناسبی برای کسب و کار شما باشد.
فولاد، آلومینیوم، روی و منیزیم متداول ترین آلیاژهای ریخته گری قالب هستند. از روش دایکاست میتوان برای ایجاد قطعات فلزی مختلف، از چرخ دنده ها و بلوک موتور گرفته تا دستگیره درها و قطعات الکتریکی استفاده کرد.
انواع فرآیندهای ریخته گری
از پرکاربردترین روش های ریخته گری فلزات میتوان به دایکاست (ریخته گری تحت فشار – دایکست)، ریخته گری ثقلی در قالب ریژه، ریخته گری ماسه ای، ریخته گری دقیق، ریخته گری کم فشار، ریخته گری گریز از مرکز، ریخته گری تحت خلا، ریخته گری کوبشی، ریخته گری لاست فوم و ریخته گری پیوسته و … در ساخت قطعات فلزی اشاره کرد.
برای تولید ریختهگریهای آلیاژی سبک، سه مورد از رایجترین فناوریها عبارتند از: ریختهگری تحت فشار بالا، ریختهگری تحت فشار گرانشی و ریختهگری تحت فشار پایین. هر فناوری میتواند از فرآیند ریخته گری دائمی با گرانش و فشار کم پشتیبانی کند. همچنین قادر به پشتیبانی از فرآیندهای ریخته گری نیمه دائمی است.
در یک فرآیند دائمی، قالب فلزی قابل استفاده مجدد میباشد. در یک فرآیند ریختهگری نیمه دائمی، قالب فلزی یک یا چند هسته شنی را در خود جای میدهد که گذرگاههای داخلی در ریختهگری نهایی را تشکیل میدهد.
مناسب بودن جهت فرآیند اتوماسیون، مزیت اصلی ریخته گری دائمی و نیمه دائمی میباشد. همچنین این مزیت منجر به تولید در مقیاس بزرگ میشود.
با توجه به کاربرد، مشخصات قطعات آلیاژی میتواند بسیار متفاوت باشد. از پیچیدگی هندسی و ضخامت دیوار گرفته تا چگالی و استحکام فلز. تمام این موارد همراه با سرعت و هزینه تولید، تعیین کنندهی انتخاب نوع فناوری ریخته گری میباشند.
تاریخچه دایکاست
صنعت چاپ در اواسط قرن نوزدهم میلادی با پیشرفت و توسعه چشمگیری مواجه شد. یکی از عوامل بسیار موثر بر رشد صنعت چاپ، اختراع تجهیزات ریخته گری تحت فشار یا دایکاست بود.
همسان بودن ابعاد، بهبود ساخت و کیفیت تجهیزات ماشین های تحریر، به وسیله ی روش دایکاست، به سرعت افزایش یافت. فرآیند پیشرفته دایکاست، باعث کاستن خطاهای تولید و همچنین افزایش سرعت متصل کردن قطعات به یکدیگر، گردید.
اولین حق ثبت اختراع مربوط به ریخته گری دایکاست در سال 1849 برای یک دستگاه کوچک دستی به منظور تولید نوع چاپ مکانیزه بود. در سال 1885، مرگنتالر ماشین Linotype را اختراع کرد. این ماشین تقریباً به طور کامل جایگزین ماشین های دستی در صنعت نشر شد. ماشین ریخته گری Soss، ساخته شده در بروکلین، نیویورک، اولین ماشینی بود که در بازار آزاد در آمریکای شمالی فروخته شد.
با صنعت ریخته گری دایکاست، تولید قطعات پیچیده در کالاهای مصرفی و لوازم خانگی، با کاهش هزینه مواجه شدند. همچنین سرعت تولید این قطعات در حجم بالا افزایش یافت.
دایکاست (ریخته گری تحت فشار) چیست؟
به فرآیند ریخته گری فلز از طریق ریختن فلز مذاب، به وسیله ی فشار بالا به داخل حفره های موجود در یک قالب دایکاست میگویند. این یک فرآیند ریختهگری دائمی است که در آن فلز مذاب با فشارهای بین 0.7 تا 700 مگاپاسکال وارد قالبی به نام «Dies» میشود.
انجماد مواد مذاب، در روش دایکاست ، در همان حالتی رخ میدهد که تحت فشار هستند. پس از طی این مرحله، تولید قطعات با استقامت بالا، صورت میگیرد.
ساخت قطعات بسیار نازک به همراه استحکام بسیار بالا، از مزایای روش دایکاست میباشد. در نظر داشته باشید که ساخت این قطعات توسط روش های دیگر ریخته گری، تقریبا امکان پذیر نمیباشد.
سرمایه ی بسیار زیادی جهت تجهیزات ریخته گری و قالب های فلزی نیاز است. در این فرآیند ساخت قطعات با استفاده از دایکاست به نسبت ساده میباشد. این فرآیند جهت انجام ریخته گری های کوچک تا متوسط مناسب میباشد.
اهداف روش دایکاست
ریخته گری یک فرآیند کارآمد و مقرون به صرفه است که میتواند طیف وسیع تری از اشکال و اجزا را نسبت به سایر روش های ریخته گری یا شکل دهی فلزات تولید کند. قطعات دایکاست معمولاً عمر طولانی دارند و عموماً برای تکمیل جذابیت بصری طراحی میشوند.
طراحان میتوانند با استفاده از قطعات دایکاست چندین مزیت به دست آورند، مانند:
- تولید با سرعت بالا: ریختهگریهای دایکستینگ را میتوان به شکلهای پیچیدهتر با تلرانسهای نزدیکتر نسبت به بسیاری از فرآیندها، به صورت انبوه تولید کرد. در بیشتر مواقع میتوان هزاران قطعه یکسان را بدون داشتن نیاز به ابزارهای اضافی، تولید کرد.
- دقت و پایداری ابعادی: دایکاست قطعات بادوام و پایداری تولید میکند و در عین حال تلرانس های نزدیک را حفظ میکند.
- محافظ EMI و RFI: قطعات دایکست در برابر گرما و UV مقاوم هستند و محافظ EMI و RFI میباشند.
- استحکام و وزن: در بیشتر موارد، قطعات دایکاست قویتر از قالبهای تزریق پلاستیک هستند و به طور کلی قویتر و سبکتر از قطعات ایجاد شده از سایر روشهای ریختهگری میباشند.
اگر به دنبال اقتصادی ترین و کارآمدترین فناوری برای تولید قطعه خود به شکل فلزی با دوام و استقامت بالا هستید، فرآیند ریخته گری تحت فشار، راه حل شما است.
این روش گسترده ترین طیف اشکال را در مقایسه با سایر تکنیک های تولید ارائه میدهد. همچنین، فرآیند ریخته گری تحت فشار، منجر به دقت بالا در مشخص شدن ابعاد، به هنگام تولید میشود.
از دیگر اهداف فرایند دایکاست عبارت هستند از:
- تولید اشکال پیچیده با تلرانس های باریک
- ریخته گری دیوار نازک فلزی
- نرخ تولید بالا
- عمر طولانی
- کمترین قیمت هر قطعه
کاربرد دایکاست چیست ؟
در بخش بالا در مورد اهداف دایکست به صورت مفصل صحبت کردیم و متوجه شدیم که ریخته گری تحت فشار، برای ساخت قطعات با شکلهای پیچیده، ساختار یکپارچه، ابعاد دقیق، سطح با کیفیت، مقاومت بالا و سختی یکی از کارآمدترین روشهای تولید است. همین علت سبب گستردگی مصرف و کاربرد در صنایع از روش دایکست شده است. یکی از صنایعی که در تولید قطعات، تجهیزات و کالای مصرفی خود از دایکاست استفاده میکند، صنعت خودرو سازی است. نزدیک به 60 درصد از قطعات بکار رفته در اتومبیل ها توسط روش ریخته گری تحت فشار تولید میشود.
از روش دایکاست در تولیدات گوناگون صنایع هوافضا، تجهیزات الکترونیکی، ساخت لوازم خانگی و جواهرسازی و … استفاده میشود. بسیاری از لوازم و قطعاتی که در زندگی روزمره با انها سروکار داریم با روش دایکست تولید شده است. مانند: قابلمه چدنی (قابلمه دایکاست) ظروف دایکاست آشپزخانه، لوازم روشنایی و چراغ دایکاست (چراغ های شهری، لوستر دایکاست خانگی)، ابزار آلات و یراق آلات، رادیاتور اتومبیل (رادیاتور دایکاست) و ….
انواع فرایندهای ریخته گری تحت فشار
فرایند ریخته گری انواع مختلفی دارد که عبارت هستند از:
- ریخته گری فشار پایین
- ریخته گری تحت خلاء
- ریخته گری فشاری
- ریخته گری نیمه جامد
انواع فرآیند ریخته گری با یک هدف یکسان طراحی شده اند. قالب گیری با استفاده از فلز مذاب تزریقی، بسته به نوع فلز ذوب شده، نوع هندسه قطعات و اندازه قطعه، صورت میگیرد.
ریخته گری تحت فشار با ایجاد قالبی شروع میشود که میتواند مکرراً در فرآیند تولید استفاده شود. ایجاد یک قالب دقیق برای طرح در حال تولید، جهت جلوگیری از خطا و استفاده مجدد با ضایعات مواد بسیار مهم است. اگر به دنبال خدمات ریخته گری دایکست در اروپا، آسیا، ایالات متحده یا جاهای دیگر هستید، ارائه دهندگان خدمات ریخته گری وجود دارند که میتوانند در ساخت قالب و ارائه خدمات تولید برای رفع نیازهای شما کمک کنند.
ریخته گری فشار بالا به کمک خلاء (Vacuum die casting)
فرآیند ریخته گری تحت فشار خلاء، بیشتر با فرآیند محفظه سرد مرتبط است. یک منبع خلاء هوا، گازهای محبوس شده در داخل حفره قالب را، قبل از ورود فلز مذاب به قالب حذف میکند.
این نوع ریخته گری دایکست تلاطم گاز را به حداقل میرساند و در کاربردهایی که برای عملیات حرارتی پس از ریختگی در نظر گرفته شده است مفید است.
برخی از مزایای این نوع ریخته گری بهبود خواص مکانیکی، پرداخت سطح بهتر، پایداری ابعادی، زمان چرخه کوتاه تر، کاهش عیوب ناشی از گازهای به دام افتاده است.
در فرآیند ریخته گری توسط فشار خلا، فلز مذاب شده با سرعت بالا به درون قالب های مادر ریخته میشود. در واقع چرخه زمانی کوتاه و دقت ریخته گری بالا در این فرآیند، از مزایای ریخته گری تحت فشار خلا محسوب میشود.
ریخته گری فشار پایین (low-pressure die casting)
اجزای آلومینیومی که حول برخی از محورهای چرخش متقارن هستند به طور قابل توجهی از ایده ریخته گری فشار پایین حمایت میکنند. چرخ های خودرو نمونه بارز ریخته گری فشار پایین هستند. در این نوع ریخته گری قالب به صورت عمودی بالای حمام فلز مذاب باقی میماند. با لوله رایزر به آن متصل میماند. سپس فلز گرم شده از 20 کیلو پاسکال تا 100 کیلو پاسکال در محفظه تحت فشار قرار میگیرد و فلز مذاب را به سمت بالا به داخل قالب میکشد.
فرآیند ریخته گری فشرده (Squeeze casting process)
ریختهگری فشاری که به نام آهنگری فلز مایع نیز شناخته میشود، دارای ویژگیهایی از ریختهگری و آهنگری برای ساخت اجزای خودرو و بدنههای ملات است. در این فرآیند ابتدا فلز مذاب در قالب فشرده میشود. سپس هنگامی که فلز مذاب شده، نواحی فرو رفته درون قالب را پر میکند، محصولات به صورت متراکم شده تولید میشوند. این روش همچنین برای ساخت کامپوزیت های زمینه فلزی مناسب میباشد، که در آن آلومینیوم مذاب به ساختار تقویت کننده الیاف نفوذ میکند.
ریخته گری فشرده باعث کاهش انقباض و تخلخل گاز، بهبود کیفیت مکانیکی به دلیل ساختار دانه های کوچک ناشی از انجماد سریع و کیفیت سطح برتر میشود. آلیاژهای آلومینیوم و منیزیم اغلب از طریق ریخته گری تحت فشار پردازش میشوند.
شکل دهی فلز نیمه جامد (Semi-solid metal forming)
شکلدهی فلز نیمه جامد (SSM)، به عنوان شکلدهی نیمه جامد، ریختهگری نیمه جامد یا پردازش حالت مخلوط شناخته میشود. نوعی فرآیند ریختهگری دایکست با قالب است که ویژگیهای ریختهگری و آهنگری را در خود دارد و از مواد نیمه مذاب استفاده میکند.
معمولاً جهت ساخت قطعات فلز آلومینیوم برای هوا فضا، پایهها و بلوکهای موتور و محفظههای فیلتر پمپ روغن استفاده میشود.
از مزایای این روش میتوان به قطعات پیچیده با دیوارههای نازک، خواص مکانیکی عالی، سطح عالی، تخلخل نسبتاً کاهش یافته و تحمل کم اشاره کرد. همچنین میتوانند منجر به عملیات حرارتی شوند. یکی از معایب این روش این است که این فرآیند به شدت در برابر عوامل محیطی مانند دما حساس است و از این رو تجهیزات تولیدی و محیطی به کنترل بیشتری نیاز دارند که منجر به استفاده از تجهیزات گران قیمت میشوند.
مراحل اجرای ریخته گری دایکاست چه هستند؟
ریخته گری فشار بالا به طور کلی شامل چهار مرحله است (die casting process) : آماده سازی قالب، تزریق قالب با فلز مذاب، خارج کردن حفره تازه ایجاد شده از قالب، و جداسازی ضایعات فلزی از حفره.
جهت ساخت قطعه در روش ریخته گری تحت فشار، ابتدا قطعات ریخته گری را آماده میکنند. قالب های دایکست از دو قسمت متحرک و ثابت ساخته میشوند. قسمت متحرک را روی صفحه متحرک و قسمت ثابت را بر روی صفحهی ثابت نصب میکنند.
تمیزکاری، روان کاری و بستن قالب از فعالیت های مهم در آماده کردن قالب های ریخته گری تحت فشار میباشند.
آماده سازی قالب، نیازمند ابعاد قطعات میباشد. با توجه به سایز دستگاه، زمان مورد نیاز جهت تمیزکاری و روان کاری متفاوت میباشد. یعنی هر چقدر ابعاد قالب و دستگاه بزرگ تر باشد، زمان بیشتری جهت تمیزکاری و روان کاری نیاز است. همچنین جهت باز و بسته کردن قالب ها، در دستگاهای بزرگ، به زمان بیشتری نیاز میباشد.
آماده سازی قالب (Mould design)
اولین مرحله ریخته گری فشار بالا، آماده سازی قالب دایکست است. در این مرحله اولیه، شرکت سازنده یک روان کننده در دیواره های داخلی قالب اعمال میکند. این امر بسیار مهم است، زیرا روان کننده دمای قالب را تنظیم میکند و در عین حال یک لایه بین فلز مذاب و قالب ایجاد میکند. در نتیجه امکان حذف راحت تر ریخته گری را فراهم میکند. برای طراحی قالب ریخته گری مناسب با فرایند خود با کارشناسان زبده فرامکانیک در تماس باشید.
قالب معمولاً از فولاد یا آلومینیوم ساخته میشود و به گونه ای طراحی میکنیم که در برابر دما و فشارهای بالا در فرآیند ریخته گری دایکاست مقاومت داشته باشد. طراحی قالب با توسعه یک طرح CAD از قالب مورد نیاز آغاز میشود. سپس از این طرح برای ایجاد یک قالب با ماشینکاری CNC استفاده میشود که بیشتر در فرآیند ریخته گری استفاده میشود.
آماده سازی متریال فلزی (Metal preparation)
مرحله بعدی آماده سازی متریال برای تزریق است. این فلز معمولاً آلیاژی مانند فولاد، آلومینیوم، منیزیم یا روی است. این فلز در کوره ذوب میشود و سپس در ملاقه ریخته میشود و آماده قرار گرفتن در قسمت تزریق دایکست است.
تزریق (Injection process)
پس از آماده سازی قالب دایکاست، شرکت سازنده، فلز مذاب را به درون قالب تزریق میکند. در این مرحله قالب باید کاملا بسته شود. در غیر این صورت، نمی تواند فلز مذاب با فشار بالا را پذیرش کند. با توجه به کاربردهای متفاوت، فلز مذاب ممکن است با فشاری بین 1500 تا 25000 پوند بر اینچ مربع (PSI) به داخل قالب تزریق شود. قالب ها، این فشار را تا زمانی که فلز مذاب سرد و جامد شود حفظ میکنند.
تخلیه حفره (Ejection)
در مرحله بعد، شرکت تولید کننده حفره تازه ساخته شده را از قالب بیرون میکشد. خود قالب معمولاً دارای پینهای اجکتوری است که وقتی درگیر میشوند، حفره را آزاد میکنند. پس از مدتی اگر فلز خام هنوز مایع باشد، شرکت سازنده باید صبر کند تا خنک شود تا بتواند حفره را از قالب خارج کند. پس از سرد شدن و سفت شدن فلز، قالب باز میشود و قطعه خارج میشود. اطمینان حاصل کنید در دایکست که قطعه قبل از دست زدن به طور کامل خنک شده است تا از آسیب احتمالی جلوگیری شود.
پرداخت نهایی (Finishing process)
آخرین مرحله ریخته گری فشار بالا، پرداخت کاری، تکان دادن یا برش کاری است. در طی این مرحله، شرکت سازنده تمام ضایعات فلزی را از حفره تازه ایجاد شده جدا میکند. زیرا غیر معمول نیست که ریخته گری تحت فشار بالا باعث تولید ضایعات فلزی اضافی شود. به عبارت دیگر، تمام مواد فلز مذاب شده برای ایجاد ریخته گری استفاده نمی شود و مقداری از فلز مذاب شده در داخل قالب گیر کرده است. در نتیجه، ضایعات فلزی باید قبل از استفاده مجدد از قالب حذف شوند.
مرحله آخر در فرآیند دایکاست، مرحله مکمل است. مرحله پرداخت نهایی مکمل کیفیت سطح است و نقش حیاتی در ریخته گری دایکاست ایفا میکند، زیرا میتواند بر دوام و عملکرد قطعه تأثیر بگذارد. فرآیندهای مکمل استاندارد شامل آنودایز، پوشش پودری، آبکاری و سخت کاری سطحی و بسیاری موارد دیگر است.
مزایای تولید قطعات از طریق روش دایکاست
ریخته گری تحت فشار یا دایکاست، نسبت به سایر فرایند های تولیدی، مزایای منحصر به فردی دارد. این مزایا منجر به صرفه جویی در قیمت قطعات و همچنین هزینه کلی تولید میشود. زمانی که شروع به ریخته گری یک قطعه میکنید، میتوانید اشکال شبکه های پیچیده را با حداقل زاویه ایجاد کنید تا عملیات ثانویه به حداقل برسد.
وقتی صحبت از تولید انبوه قطعات فلزی میشود، ریخته گری قالب دایکست یکی از کارآمدترین و مقرون به صرفه ترین روش ها است. این فرآیندی است که برای قرن ها وجود داشته است، اما محبوبیت آن در سال های اخیر افزایش یافته است زیرا تولیدکنندگان به دنبال راه هایی برای کاهش هزینه های تولید هستند.
همچنین میتوانید چندین بخش را درون یک قطعه ترکیب کنید. عملیات مونتاژ را حذف کرده و هزینه های نیروی کار را کاهش دهید.
- طراحی همه کاره: ریخته گری دایکست میتواند تقریباً هر اندازه قطعات هندسی، بافت سطح یا درخشندگی را ایجاد کند.
- حداقل مونتاژ: ویژگی های مونتاژ مانند گل میخ ها، سوراخ های مته را میتوان در طراحی قالب ادغام کرد.
مزیت و مزایای دایکستینگ
- قطعات دایکاست نسبتا ارزانتر هستند و کیفیت یکنواختی را برای تولید با حجم زیاد تولید میکنند. هزینه های کمتر نیروی کار به دلیل فرآیندهای نیمه خودکار یا کاملاً خودکار است.
- اشکال پیچیده: دایکاست فرآیندی است که میتواند اشکال پیچیده با تلرانسهای محدود تولید کند
- فرم های پیچیده و اشکال پیچیده را میتوان به راحتی با دایکست ریخته شود، با اندازه قطعات از 25 گرم تا 25 کیلوگرم.
- سرعت تولید بالا: این یک فرآیند نسبتا سریع است، که میتواند یک مزیت در زمانی که زمان اهمیت دارد
- از آنجایی که فلز مذاب به سرعت در دیواره های قالب خنک میشود، قالب ریخته گری دارای پوسته ریزدانه سخت با استحکام عالی است. در نتیجه، با کاهش ضخامت دیواره، نسبت مقاومت به وزن اجزای دایکاست افزایش مییابد.
- مقرون به صرفه: این فرآیند همچنین نسبتاً ارزان است و آن را به گزینه ای مقرون به صرفه برای بسیاری از برنامه ها تبدیل میکند.
- قطعات با دیوارههایی به نازکی 0.38 میلیمتر به دلیل فشار زیاد مورد استفاده در طول فرآیند امکانپذیر است.
- تطبیق پذیری: این فرآیند همه کاره است و میتوان از آن برای ریخته گری انواع فلزات از جمله آلومینیوم، روی و منیزیم استفاده کرد.
- سطوح صاف را برای یاتاقان هایی که در غیر این صورت ماشین کاری میشوند ایجاد میکند.
- این میتواند محصولاتی به شکل خالص با نرخ های بالا تولید کند که نیاز به پس پردازش کمی یا بدون نیاز دارند.
- دقت ابعادی عالی و کیفیت سطح خوب – 0.8-3.2 um Ra.
- قطعات کوچکتر را میتوان با استفاده از قالب چند حفره یا ریخته گری مینیاتوری تولید کرد.
- تکرارپذیری: همچنین به درجه بالایی از تکرارپذیری اجازه میدهد، به این معنی که قطعات را میتوان با مشخصات دقیق تولید کرد.
مزایای دیگر عبارتند از:
- افزایش دقت در ابعاد ( با توجه به مواد ریخته گری)
- سطوح ریخته گری صاف
- ریخته گری دیوار های نازک تر در مقایسه با ماسه و قالب های دائمی
- قابلیت ریخته گری درج ها
- تولیدات انبوه
- تولیدات مقرون به صرفه
- تولید قطعات مرغوب با سطح مقاطع نازک
- تولید قطعات پیچیده
- توانایی تولید قطعات به صورت سری
- بهبود پرداخت قطعات تولید شده
- استحکام بالای قطعات تولید شده
- افزایش تولید قطعات در مدت زمان کوتاه
- توانایی تحمل سخت تر
- کوتاه شدن تعداد مراحل تولید فرایند
- زمان چرخه تولید سریع
- کاهش ضایعات مواد
معایب روش دایکاست چیست؟
دایکاست یا ریخته گری تحت فشار، در مقایسه با سایر فرآیندهای ریخته گری تا حدودی گران است. به نوع خاصی از دستگاه ریخته گری نیاز دارد که خرید و نگهداری آن گران میباشد. شرکت های تولیدی میتوانند با انتخاب روی به عنوان ماده ریخته گری در هزینه های خود صرفه جویی کنند. اما دایکاست همچنان یک فرآیند ریخته گری نسبتاً گران به حساب میآید.
عیب اصلی ریخته گری با دایکاست نیاز به سرمایه بسیار بالا است. هم تجهیزات ریخته گری مورد نیاز و هم قالب ها و اجزای مربوطه در مقایسه با سایر فرآیندهای ریخته گری بسیار پرهزینه هستند.
بنابراین، برای اینکه ریخته گری دایکاست به یک فرآیند اقتصادی تبدیل شود، به حجم تولید زیادی نیاز است. معایب دیگر عبارتند از:
افزایش نرخ ضایعات میتواند ناشی از شکست سیالیت باشد، و هزینه های ضایعات در ریخته گری بالا است.
ریخته گری دایکاست شامل تعداد زیادی قسمت است. بنابراین از اهمیت ویژه ای برخوردار است.
در فرآیند ریخته گری دایکاست استاندارد، ریخته گری نهایی دارای مقدار کمی تخلخل خواهد بود. این عمل مانع از اقدام هر گونه عملیات حرارتی و جوشکاری میشود. زیرا گرما موجب انبساط گاز موجود در منافذ میشود که باعث ایجاد ترک های ریز داخل قطعه و لایه برداری سطح میشود. با این حال، برخی از شرکت ها راه هایی برای کاهش تخلخل قطعه پیدا کرده اند که اجازه جوشکاری و عملیات حرارتی محدود را میدهد.
بنابراین یک عیب مربوط به دایکاست این است که فقط برای قطعاتی مناسب است که نرمی در آنها قابل قبول است. قطعاتی که نیاز به سخت شدن و تمپر دارند در قالب ها ریخته نمیشوند.
معایب دایکستینگ
- قطعات ریخته گری دایکاست تنها برای دسته های تولیدی بزرگ به دلیل هزینه بالای تجهیزاتشان مقرون به صرفه هستند
- فلزات و آلیاژهای با نقطه ذوب بالا مناسب نیستند
- به دلیل محتوای آهن، فلزات آهنی مانند فولاد ضد زنگ، فولاد کربنی و فولاد آلیاژی تمایل به زنگ زدگی دارند، بنابراین مناسب نیستند.
- قطعات بزرگ به دلیل محدودیت در طراحی قالب و فرآیند ریخته گری امکان پذیر نیست
- هزینه قالب بالا و به طور کلی زمان طولانی.
- تغییرات در طراحی قطعه زمان بر و پرهزینه است، بنابراین ارزش نمونه سازی قطعه را قبل از انجام دایکستینگ دارد.
- تخلخل ناشی از هوا و گازهای محبوس شده بر یکپارچگی قطعه تأثیر میگذارد. ریخته گری تحت خلاء با ایجاد خلاء قبل از پر شدن فلز مذاب تخلخل را کاهش میدهد.
- ریخته گری دارای مشخصات وزنی مخصوص به خود میباشد که ریخته گری دایکاست باید به آن پایبند باشد. به عنوان مثال، یک ریخته گری معمولی ممکن است به وزنی بین 1 اونس تا 15 پوند نیاز داشته باشد. اگر وزن ریخته گری بیشتر یا کمتر باشد، دچار نقص میشود.
انواع ماشین های دایکاست
دستگاه ریخته گری دایکست را میتوان با توجه به روش های طبقه بندی مختلف، مانند کاربرد و اندازه، دسته بندی کرد. به طور کلی دستگاه های ریخته گری را میتوان به دو نوع محفظه گرم و اتاق سرد طبقه بندی کرد.
دستگاه دایکاست با محفظه گرم (Hot chamber die casting machine)
دستگاه های دایکاست محفظه گرم، دارای یک محفظه فشار هستند که به حفره قالب متصل میباشند. فلز مذاب میتواند به طور مداوم به داخل محفظه توسط فشار نفوذ کند. هنگامی که سیلندر محفظه به حالت بدون فشار باز میگردد، فلز مذاب به داخل قالب ریخته گری وارد میشود. ظرف مخصوص قالب، جهت ذوب کردن فلز به دستگاه متصل میشود و مکانیزم پیستونی برای تزریق هیدرولیک فلز به داخل قالب ظرف آهنگری نصب میشود. برخی از ماشین های ریخته گری محفظه داغ، از هوای فشرده برای فشار مستقیم فلز به داخل قالب استفاده میکنند.
دستگاه ریخته گری محفظه داغ بیشتر برای آلیاژهایی با دمای ذوب پایین مانند روی، قلع و سرب استفاده میشود (دمای زیر ۴۰۰ درجه سانتیگراد). دماهای لازم برای ذوب سایر آلیاژها مانند فولاد به پمپ که در تماس مستقیم با فلز مذاب است آسیب میرساند.
فشار تزریق معمولی برای دستگاه ریخته گری محفظه داغ بین 1000 تا 5000 psi (بین 69 تا 345 بار) است.
استفاده از مکانیزم پیستون مورد نیاز نیست زیرا مکانیسم تزریق در فلز مذاب غوطه ور است. بنابراین لازم است از حمله شیمیایی یا فرسایش، به سیستم تزریق غوطه ور جلوگیری شود.
فرآیند ریخته گری دایکست فلزاتی از جمله روی و قلع که نقطه ذوب کمتری نسبت به سایر فلزات دارند، در دستگاه ریخته گری با محفظه داغ، صورت میگیرد.
ویژگی های دستگاه ریخته گری محفظه داغ
ویژگی های مثبت و منفی این نوع دستگاه های دایکست عبارت هستند از:
مزایای ریخته گری محفظه داغ
- بهره وری بالا
- بهبود سطح پرداخت
- قابلیت تولید ریخته گری های پیچیده
- تحمل ابعاد نزدیک
- مناسب برای ساخت قطعات ریخته گری روی
- سرعت تولید سریعتر را ارائه میکند – تا 18000 ضرب در ساعت برای قطعات کوچکتر.
- قطعاتی با تخلخل کاهش یافته تولید میکند
- فلز را درون دستگاه ریخته گری ذوب میکند
- این فرآیند حداقل ضایعات را ایجاد میکند
- عمر طولانی تر به دلیل نقطه ذوب پایین
معایب ریخته گری محفظه داغ
- مقرون به صرفه فقط برای دسته تولید با حجم بالا (مناسب تولیدات تعداد پایین نیست)
- فلزات با نقطه ذوب بالا را نمیتوان استفاده کرد
- محدوده فشار بالا مورد نیاز است
- سیالیت کم فلز در نتیجه پیچیدگی محصول را محدود میکند
- مسائل مربوط به عملیات حرارتی
- ممکن است علائم اجکتور و مقدار کمی فلاش در خط جداکننده قالب باقی بماند.
اجزای دستگاه دایکاست با سیستم تزریق محفظه گرم
- سیلندر هیدرولیکی
- پلانجر
- مجرای ورودی
- محفظه شات تزریق
- فلز مذاب
- کوره
- دیگ
- مجرای گردن غازی یا «گوس نک» (Gooseneck)
- بخش ثابت قالب
- بخش متحرک قالب
- صفحه متحرک
- میله افقی نگهدارنده
- واحد باز و بسته کردن قالب یا «کلمپینگ» (Clamping)
- صفحه ثابت
- سیستم پران (جدا کننده قطعه از قالب)
- میله سیستم کلمپینگ
- صفحه پشتی
با بسته شدن قالب ها، پیستون خارج شده و دریچه محفظه را باز میکند تا فلز مذاب به داخل محفظه جریان یابد. سپس پیستون در حالی که فلز مذاب را از طریق گردن غاز و نازل به داخل حفره قالب فشار میدهد، درگاه را مسدود میکند. پس از ورود به حفره قالب، فلز مذاب تحت فشار نگه داشته میشود تا زمانی که در داخل قالب جامد شود. فرآیند محفظه گرم به دلیل فشار بالا، نرخ تولید بسیار بالاتری نسبت به فرآیند محفظه سرد دارد. ریخته گری محفظه گرم برای برخورد با فلزات با نقطه ذوب پایین تر مانند قلع و روی و همچنین آلیاژها مناسب تر است.
دستگاه دایکاست با محفظه سرد (Cold Chamber Die Casting Machine)
در دستگاه ریخته گری دایکاست با محفظه سرد (Cold Chamber Die Casting Machine)، فلز مذاب از یک کوره نگهدارنده جداگانه، پس از بسته شدن قالب به داخل محفظه سرد ریخته میشود. سپس فلز با فشار وارد قالب میگردد. پس از انجماد قالب را باز میکنیم، مواد به قسمت ریخته گری تزریق میشود.
فلز در خارج از دستگاه ذوب میشود و سپس به محفظه فشرده سازی اضافه میشود. با توجه به جهت حرکت پیستون فشرده سازی، میتوان آن را به دستگاه ریخته گری دایکست محفظه سرد عمودی و دستگاه ریخته گری اتاق سرد افقی تقسیم کرد.
فلز مذاب از کوره دستگاه ریخته گری محفظه سرد عمودی خارج شده و به داخل محفظه فشرده سازی ریخته میشود. فلز توسط پیستون تراکمی به درون قالب های مخصوص داخل میشود و فلز اضافی توسط پیستون دیگری به بیرون رانده میشود.
دستگاه ریخته گری دایکست افقی محفظه سرد به همان روش دستگاه ریخته گری دایکست عمودی کار میکند، اما جهت حرکت پیستون افقی است. اکثر ماشین های ریخته گری مدرن افقی هستند.
دستگاه ریخته گری اتاق سرد میتواند برای فلزات با نقطه ذوب زیاد، مانند فلز مس مناسب باشد.
ویژگی های دستگاه ریخته گری محفظه سرد
ویژگی های مثبت و منفی این نوع دستگاه های دایکست عبارت هستند از:
مزایای ریخته گری دایکاست محفظه سرد
مزایای دستگاه ریخته گری محفظه سرد عبارت هستند از:
- کاهش احتمال خوردگی
- مناسب برای ریخته گری آلومینیوم، مس و آلیاژهای آنها
- قابل استفاده برای ساخت قطعات بزرگ
- قطعات با مقاومت بالاتر
- ریخته گری فلزی متراکم تر به دلیل افزایش فشار در حین تزریق
- هزینه نگهداری کمتر
- دقت ابعادی استثنایی را برای قطعه به ارمغان میآورد.
- امکان تولید با سرعت بالا
- فرآیند ساده برای انجام
معایب ریخته گری دایکاست محفظه سرد
- زمان چرخه کندتر از ریخته گری در اتاق گرم.
- ممکن است به دلیل انتقال فلز از کوره به محفظه باشد.
- سطح اکسیداسیون و سایر آلاینده ها در فرآیند بالا باقی میماند.
- کیفیت قسمت نهایی به دلیل آلاینده ها بیشتر در معرض تأثیر قرار میگیرد.
- فرآیند ریخته گری فشار پایین
اجزای دستگاه دایکاست با سیستم تزریق محفظه سرد
- سیلندر هیدرولیکی
- حفره ریختن مواد مذاب
- فلز مذاب
- پاتیل
- پلانجر
- محفظه شات
- بخش ثابت قالب
- بخش متحرک قالب
- صفحه متحرک
- میله افقی نگهدارنده
- کلمپینگ
- صفحه ثابت
- غلاف تزریق
- اسپرو یا راهگاه
- سیستم خروج قطعه
- میله کلمپینگ
- صفحه پشتی
فرآیند محفظه سرد زمانی شروع میشود که مواد مذاب از طریق سوراخ ریختن از کوره به محفظه شات منتقل میشود. سپس یک پیستون هیدرولیک درگاه محفظه سرد را میبندد و فلز را با فشار وارد حفره قالب میکند. فشار تزریق معمولی برای دستگاه ریخته گری اتاق سرد بین 2000 تا 20000 psi است (محدوده فشار بین 30 مگاپاسکال تا 150 مگاپاسکال است). پس از تزریق فلز مذاب به داخل حفره قالب، پیستون به سمت جلو باقی میماند و فشار را نگه میدارد در حالی که ریختهگری جامد میشود. پس از انجماد، سیستم هیدرولیک پیستون را جمع میکند و قطعه میتواند توسط واحد گیره خارج شود. واحد گیره و نصب قالب ها مشابه دستگاه محفظه گرم است.
انتخاب روش ریخته گری مناسب
حال سوال ایجاد میشود که کدام نوع دستگاه ریخته گری دایکست را باید انتخاب کنید؟ شما میتوانید دستگاه را بر اساس فلزاتی که میخواهید استفاده کنید انتخاب کنید.
برای مثال، اگر میخواهید ریختهگری روی، قلع و سرب تهیه کنید، باید یک دستگاه ریختهگری با محفظه داغ انتخاب کنید، زیرا به راحتی از خوردگی رنج میبرد و برای آلیاژهایی با دمای ذوب پایین و سیالیت مناسبتر است. علاوه بر این، دمای بالای مورد استفاده در ریختهگری آلیاژهای آلومینیوم و مس، عمر دستگاههای محفظه گرم را کوتاه میکند.
برعکس، دستگاه ریخته گری محفظه سرد برای ریخته گری فلزات با نقطه ذوب بالا مانند آلومینیوم یا آلیاژهایی با محتوای آلومینیوم بالا مناسب ترند.
مشخصات دستگاه دایکاست محفظه سرد و گرم
هر دو دستگاه ریخته گری محفظه گرم و سرد معمولاً با تناژ نیروی گیره مشخص میشوند. نیروی گیره مورد نیاز توسط ناحیه پیش بینی شده قطعات در قالب و فشاری که فلز مذاب با آن تزریق میشود، تعیین میشود. بنابراین، بخش بزرگتر به نیروی گیره بزرگتری نیاز دارد. همچنین، مواد خاصی که نیاز به فشار تزریق بالا دارند، ممکن است به ماشینهای تناژ بالاتری نیاز داشته باشند. اندازه قطعه باید با سایر مشخصات دستگاه مانند حداکثر حجم شات، ضربه گیره، حداقل ضخامت قالب و اندازه صفحه مطابقت داشته باشد.
قطعات دایکست میتوانند از نظر اندازه بسیار متفاوت باشند و بنابراین برای پوشش دادن محدوده بسیار وسیعی به این اقدامات نیاز دارند. در نتیجه، ماشینهای ریختهگری دایکست به گونهای طراحی شدهاند که هر کدام محدوده کوچکی از این طیف وسیعتر از مقادیر را در خود جای دهند. مشخصات نمونه برای چندین دستگاه ریخته گری محفظه گرم و سرد محفظه سرد در زیر آورده شده است.
دایکست
Type |
نیروی گیره
Clamp force (ton) |
بیشینه حجم سیال مذاب در هر ضربه Max. shot volume (oz.) |
کورس گیره
Clamp stroke (in.) |
حداقل ضخامت قالب
Min. mold thickness (in.) |
اندازه صفحه
Platen size (in.) |
Hot chamber | 100 | 74 | 11.8 | 5.9 | 25 x 24 |
Hot chamber | 200 | 116 | 15.8 | 9.8 | 29 x 29 |
Hot chamber | 400 | 254 | 21.7 | 11.8 | 38 x 38 |
Cold chamber | 100 | 35 | 11.8 | 5.9 | 23 x 23 |
Cold chamber | 400 | 166 | 21.7 | 11.8 | 38 x 38 |
Cold chamber | 800 | 395 | 30.0 | 15.8 | 55 x 55 |
Cold chamber | 1600 | 1058 | 39.4 | 19.7 | 74 x 79 |
Cold chamber | 2000 | 1517 | 51.2 | 25.6 | 83 x 83 |
مقایسه دایکاست و قالب گیری تزریقی
در واقع، فرآیند و مراحل قالب گیری تزریقی و ریخته گری دایکست مشابه است. تفاوت اصلی دایکاست و قالب گیری تزریقی در نوع و مقدار مواد استفاده شده است. همچنین هر کدام، مزایا و معایب خاص خود را دارند. حال سوال ایجاد میشود که کدام را انتخاب کنیم؟ اگر مشخص کرده اید که از چه نوع ماده ای استفاده کنید، پاسخ واضح است، اما اگر نمیدانید چه ماده ای باید استفاده کنید، باید در مورد این دو تکنیک بیشتر بدانید.
تفاوت اصلی
بهتر است بدانید که در فرایند دایکاست از مواد خام فلزی استفاده میکنند، اما همانطور که میدانید در قالب گیری تزریقی از پلیمر یا پلاستیک استفاده میشود.
مزایای دایکستینگ:
- دقت بالا و تحمل سخت تر
- طرح های پیچیده را میتوان به راحتی ریخته گری کرد
- قالبهای دایکاست قویتر، سفتتر، پایدارتر و مقاومتر از قالبهای تزریق پلاستیک هستند.
- ریخته گری های فلزی در برابر اشعه ماوراء بنفش، هوازدگی و ترک خوردگی کاملا مقاوم هستند.
مزایای قالب گیری تزریقی:
- قطعات قالبگیری شده پلاستیکی ممکن است بر اساس حجم واحد ارزانتر باشند.
- قطعات قالب گیری تزریق پلاستیک، عایق های الکتریکی خوبی به حساب میآیند.
- انعطاف پذیری بالاتر در فرآیند قالب گیری تزریقی.
- مواد مختلف پلاستیکی یا پلیمری را درون خود میتوانند جای دهند.
- از پرکننده ها میتوان در قالب های پلاستیکی برای افزایش استحکام استفاده کرد.
ریخته گری برای ساخت قطعات و سازه های فلزی
مدت زمان چرخه انتقال فلز مایع به داخل دستگاه ریخته گری، میتواند از پروژه ای به پروژه دیگر متفاوت باشد. برخی از چرخه ها میتوانند یک ثانیه یا کمتر طول بکشند، برخی میتوانند دو تا سه دقیقه طول بکشند. پس از انجماد فلز، در داخل حفره قالب، قالب توسط گیره هیدرولیک، آزاد میشود. سپس به سیستم تخلیه اجازه میدهد تا ریختهگری از طریق قالب خارج شود. پس از آن ریختهگریها به مرحله بعدی فرآیند منتقل میشوند تا مواد اضافی مانند دروازهها، رانرها، سرریزها و فلاشها، از قطعه حذف شوند.
فرآیند ریخته گری یک فرآیند کارآمد برای تولید انبوه قطعات و سازه های فلزی با هندسه ها و اشکال پیچیده است. این فرآیند به طور گسترده در بسیاری از صنایع مدرن مانند خوشه خودرو استفاده میشود که در آن بهره وری یکی از محرک های تجاری مهم است. این فرآیند جهت تولید دسته های بزرگی از قطعات و اجزا مورد توجه قرار میگیرد.
دایکاست برای تولید قطعات در مقیاس بزرگ با هزینه کم مناسب است. ریخته گری یک فناوری بسیار مهم جهت ساخت فلز در بسیاری از زمینه های صنعتی مدرن است. برای انجام یک توسعه فرآیند دایکستینگ عملی و کارآمد، شبیهسازی CAE صورت گرفت.این یک روش کارآمد برای کاهش زمان طراحی و توسعه است.
یک مطالعه موردی مبتنی بر شبیه سازی از طراحی فرآیند ریخته گری دایکاست جهت نشان دادن کارایی آن ارائه شد. از طریق این مطالعه موردی، نحوه استفاده از شبیهسازی عددی جهت آشکارسازی ارتباط بین متغیرهای خروجی فرآیند ریختهگری، مدلسازی و شبیهسازی واقعی ارائه گردید.
مواد ریخته گری درون قالب ها
در سالیان گذشته، انسان به تولید و استخراج فلزات دسترسی نداشت. اما به مرور زمان، با کشف فلزات، روش های مختلفی جهت تهیه قطعات فلزی به دست آمد. با اینکه میتوان هم مواد آهنی و هم غیر آهنی را داخل قالب ها ریخت، اما بهتر است بدانید که همه مواد برای ریختهگری با قالب مناسب نیستند. زیرا این فرآیند نیازمند حرارت دادن مواد تا نقطه ذوب و سپس فشار دادن آن به قالبهایی که قابلیت استفاده مجدد دارند، میباشد.
1- آلومینیوم
به دلیل ماهیت کم هزینه آلومینیوم، به طور گسترده ای در فرآیند ریخته گری استفاده میشود. آلومینیوم دایکاست سبک و سازگار با محیط زیست است. به تولیدکنندگان این امکان را میدهد که قطعاتی با دیواره های نازک و هندسه های پیچیده تولید کنند. قطعات آلومینیومی به دلیل مقاومت در برابر خوردگی و هدایت حرارتی – الکتریکی، کاربردهای مختلفی در صنایع هوافضا، خودروسازی و الکترونیک دارند.
2- فلز روی
ریخته گری روی برای اقلامی که به استحکام و شکل پذیری افزایش یافته، دقت بالا، تحمل سخت و ویژگی های حرارتی برجسته نیاز دارند ایده آل است. رایج ترین نمونه های اقلام ریخته گری روی چرخ دنده ها و اتصال دهنده ها هستند.
برای بهبود کیفیت محصول نهایی، ممکن است نیاز به ترکیب روی با آلومینیوم باشد. به دلیل نقطه ذوب پایین این فلز، فرآیند ریخته گری روی، در یک اتاق گرم ایده آل صورت میگیرد.
3- فلز مس
تقریباً تمام اقلام ساخته شده از مس بادوام هستند. علاوه بر این، مس مقاومت بالایی در برابر خوردگی دارد. در نتیجه، به طور گسترده ای برای تولید قطعات جهت صنایع لوله کشی و برق استفاده میشود.
4- منیزیم
منیزیم یک فلز ایدهآل جهت ریختهگری با قالب در مواقعی که به دیوارههای نازک و دقت بالا نیاز است، میباشد. منیزیم سبک وزن است از این رو به طور گسترده در صنعت هوافضا استفاده میشود.
5- آلیاژهای روی
آلیاژهای روی مانند آلیاژهای ZA و آلیاژهای زاماک بسیار آسان ریختهگری میشوند. واکنش آنها نیز به دلیل افزایش استحکام برای این فرآیند بسیار ایدهآل است. آلیاژهای روی به طور کلی به عنوان یک جایگزین تزئینی و کاربردی برای آهن و برنج استفاده میشوند.
6- آلیاژهای برنز و برنج
آلیاژهای برنز و برنج ممکن است تقریباً به همان سرعت آلیاژهای روی ریخته گری شوند. آلیاژهای برنز و برنج تولید کننده را قادر میسازد تا قطعات بادوام را با کارایی بهتر بسازد.
7- آلیاژهای سرب
آلیاژهای سرب برای تولید وسایل ایمنی آتش نشانی، اقلام فلزی زینتی و یاتاقان ها استفاده میشوند. بدون شک، استفاده از این نوع آلیاژها به دلیل توانایی آنها در برابر مقاومت با خوردگی است. استفاده از آنها در کالاهایی که با مواد غذایی در تماس هستند توصیه نمی شود.
عیوب ریخته گری دایکاست
ایجاد حفره و عیوب در روش دایکاست کاملا طبیعی بوده که شناخت این عیوب ما را در جهت رفع انها کمک میکند. این عیوب شامل: ایجاد زائدههای ناخواسته بر روی قطعه، پر نشدن کامل حفرههای قالب، ایجاد حباب، تشکیل ترکهای گرم (ترکهای ناشی از جمع شدگی) و باقی ماندن اثر پین پران بر روی قطعه از عیب و نقصهای احتمالی در فرآیند ریخته گری تحت فشار هستند.
از انجایی که روش دایکاست روشی دقیق بوده، پس با بررسی و نظارت کافی بر روی قطعات و قالب میتوان به قطعهای با کیفیت بالا دست یافت. هنگامی که مساعل فنی و محاسباتی و اجرایی را به درستی اجرا نکنیم، باید افزایش احتمال ایجاد عیب و نقصهای مذکور در قطعه را داشته باشیم.
در قسمت زیر به بررسی علت ایجاد عیب ها و راه حل برطرف کردن عیوب دایکاست میپردازیم:
- زائدههای ناشی از بیرونزدگی مواد مذاب: زیاد بودن فشار تزریق و یا کم بودن نیروی لازم برای بسته نگه داشتن بخش متحرک قالب
- عدم پر شدن کامل حفرهها: کافی نبودن حجم شات تزریق، کم بودن سرعت تزریق و یا پایین بودن دمای مواد در حین تزریق
- تشکیل حباب در ساختار قطعه: بالا بودن دمای مواد در حین تزریق و یا عدم یکنواختی نرخ خنک شدن
- ایجاد ترک گرم: یکنواخت نبودن نرخ خنک شدن
- ایجاد علامت در حین خروج قطعه: کم بودن زمان خنک شدن و یا بالا بودن نیروی خروج
نرخ خنک شدن مواد مذاب و میزان یکنواختی نرخ سرمایش، دلیل بسیاری از عیوب ریخته گری تحت فشار هستند. عواملی که به طور مستقیم بر روی نرخ خنک کاری و سرمایش تاثیر میگذارد عبارتند از : یکنواختی ضخامت دیواره و یکنواختی دمای قالب
دیدگاهتان را بنویسید